Christian Daniel
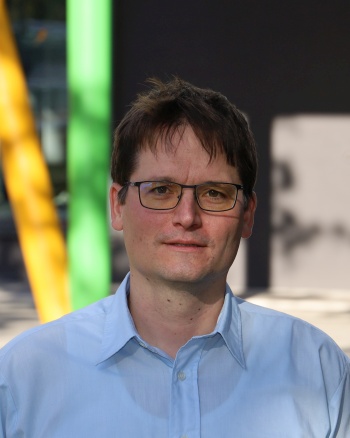
Dr.-Ing. Christian Daniel
Mehrkörperdynamik (IWTM)
Current projects
Competence in electromobility: sub-project "Digital twin for powertrain concepts (DZA) with variable modeling depth"
Duration: 01.01.2024 bis 31.12.2027
The project aims to implement a digital twin in the powertrain area and combines various methodological preliminary work in the area of component development (interaction between structural and electrodynamics as well as acoustics in e-components) with overall system considerations. The main focus of the work is on simulation models for constant velocity joints in the drivetrains, which are subject to different loads as a result of e-mobility.
Questions relating to the identification of excitation mechanisms in the constant velocity joints and process parameters for influencing them are being investigated. The necessary experimental investigations are carried out on a cardan shaft test bench and a road-to-rig test bench.
The relevant work packages can be summarized as follows:
- Recording of measurement data (forces, torques, deflection angles, vibrations) of the drivetrain in cooperation with the Institute for Competence in AutoMobility (IKAM) & the Center for Method Development (CMD)
- Development of a detailed calculation method for the drivetrain with a focus on the constant velocity joints
- Reduction of the degree of complexity for implementing the method in the typical development process
This text was translated with DeepL
Completed projects
Determination of the mechanical properties of the sacroiliac joint of a dog by imaging measurement methods and model update in a multi-body model
Duration: 01.01.2023 bis 31.12.2024
The sacroiliac joint (SIG) is the articulated connection between the sacrum and the ilium, whereby the joint is characterized by a composite structure and is tight and only slightly mobile as a result of various attaching ligaments. In many dogs, this joint stiffens further with age, causing pain during movement. So far, too little information is known about the degree of stiffening and the actual range of movement for treatment.
Consequently, recording the range of motion of different individuals (healthy and diseased) is a necessary step towards a better understanding of the so-called SIG syndrome.
The basic examination of the mechanical properties of the SIG is carried out post mortem. To determine the mobility of the joint, the sacrum is fixed and a movement is forced on the ilium using actuators. The forces required for this and the resulting spatial movement of the ilium and sacrum are measured. In principle, the translational and rotational stiffnesses of the SIG can be determined from the ratio of the kinematic and dynamic variables determined in this way.
As it is not possible to impose directed loads on the ilium to specifically stress the individual ligaments of the joint, the elastic parameters of the ligaments are determined using heuristic methods from the previously determined measurement data. This method is validated by simulation using a multi-body model that includes the ilium, the ligaments and the actuators of the test stand with their spatial orientation.
This text was translated with DeepL
Vibration analysis of a refrigeration system
Duration: 01.04.2024 bis 31.12.2024
In refrigeration systems, gaseous media are compressed by a compressor and thereby liquefied. The refrigerant is then transported in pipes to other components such as heat exchangers or dryers. The rotary motion of the compressor causes vibration excitation of the pipe system, whereby resonance excitation is also possible depending on the speed and operating point, which can lead to large deformations and system failure, especially in the often weakly damped pipes.
In the project, the vibrations of a piping system are determined experimentally and a 3D FE model of the actual state is created. After validation, design changes in the fastening and mounting of the pipes can be examined for their influence on the stresses acting in the material. Particularly in complex refrigeration systems, the pipelines are very long and angled, which is why an analytical approach is no longer possible.
This development step allows critical pipe vibrations to be determined and suitable design changes to be implemented in the calculation model. In practice, virtual product development saves the construction of prototypes and reduces the final test to a few preferred variants that can be derived from the calculation model.
This text was translated with DeepL
Optimization of the hammer throw using parameterized synthetic motion kinematics in a multi-body model
Duration: 01.07.2022 bis 30.06.2024
The sport of hammer throwing is a very technical discipline in which the execution of the movement significantly influences the result, i.e. a high throwing distance. There are many approaches for supporting technical training that are based on metrological data and image acquisition. The accelerations and locus curves of the athlete and hammer are recorded and can be compared with target data. Multi-body simulation of the hammer throw, in which the kinematics of the hand movement are described by means of a parameterized synthetic trajectory, allows the movement of the hammer and thus the final throwing distance to be simulated. Scalar parameters in the approach allow the trajectory to be changed and thus the direct analysis of changes in movement. Using heuristic methods, the parameters of the hand movement can thus be optimized for a maximum throwing distance and the motion sequences derived from this can then be used to improve training.
This text was translated with DeepL
Airborne and structure-borne noise testing on agricultural vehicles
Duration: 01.01.2024 bis 30.04.2024
Due to the necessary high performance requirements, agricultural commercial vehicles are often equipped with large diesel engines that drive numerous units. During the operation of such a vehicle, the engine generates very dominant structure-borne and airborne noise emissions, which is why working next to a running large diesel engine is usually not possible without hearing protection. For this reason, modern driver's cabs in current vehicles are heavily encapsulated so that the driver is protected from airborne noise. However, technical modifications to the engine can lead to a subjective increase in sound amplitudes in a limited frequency range, which is perceived as disturbing in the driver's cab.
As part of the experimental study, the cause of the noise is narrowed down and specific conversion measures on the cabin are evaluated. In addition to the vibration acceleration on engine parts, the sound pressure outside and inside the cabin is recorded and evaluated audiologically, among other things.
This text was translated with DeepL
Development of an electric boat with air gap motor
Duration: 01.02.2021 bis 30.06.2023
In recent years, electrical machines have been developed and optimized at OVGU in various research projects (ELISA, KEM - Kompetenz in Elektromobilität). The basic design is a permanently excited synchronous motor with an air gap winding, which requires particularly little copper. The current design is an external rotor, i.e. the stator is inside and the outer part rotates. The advantage of this design is a higher torque due to the large diameter of the air gap, which means that a gearbox is not required to connect the motor to the wheel or the propeller.
While the central element of the investigations as part of the KEM research project was the optimization of the thermal and acoustic properties of the motor, current and future projects are investigating an adapted design to make the manufacturing process more efficient, as well as the adaptation to corresponding applications.
After an early version of the motor had already been installed in an e-glider, test drives revealed a need for further optimization, primarily with regard to the construction of the fuselage shell. The second version of the e-glider is characterized by consistent lightweight construction, which is realized with an extremely light fuselage shell by FVK Dessau. In addition, the drivetrain is being adapted with the electric motor with air gap winding, which was optimized as part of the research project and will become part of an outboard drive.
Technical data: E-glider Adelheid 2
- Propulsion: outboard motor
- Motor: optimized electric motor with air gap winding and 12 kW continuous power, water-cooled - electrically limited to 10 kW
- Traction battery: 3x2 kWh 48 V LiIo
- Motor controller: 1x Hersi HST350 air-cooled
- Empty weight: approx. 250 kg
This text was translated with DeepL
Dynamic vibration test of a battery module
Duration: 01.08.2022 bis 30.11.2022
As part of the KEM - Competence in Electromobility research project, a modular battery pack based on 48V was developed, which is characterized above all by good dismantlability and temperature control of the cells. However, these functions require a complex structure that must be able to withstand the dynamic loads (depending on the application) during operation.
To ensure functionality under dynamic conditions, a vibration test was carried out in accordance with ECE R100-R2, whereby a 10 kN shaker including a suitable vibration control system was used due to the forces required (as a result of the high mass to be moved). In order to check all hose connections for leaks during the vibration test, the battery module was continuously flushed with cooling medium.
As a result, the battery module tested showed no structural damage or leaks after several cycles (sine sweep 7-50 Hz; 1-0.2 g peak).
This text was translated with DeepL
Optimization of the topology of lattice structures to increase structural damping
Duration: 01.01.2022 bis 31.10.2022
As part of a collaboration with the Alfred Wegener Institute (AWI), lattice structures (lattice arrangements of individual small strings) that are used as bearings in machines were investigated. Previous studies have shown that the arrangement of the strings has a significant influence on the stiffness of the structures and that irregular designs are preferable in this context. Since the vibration behavior of technical systems is determined by the damping behavior, especially with regard to the amplitudes near resonance, the current project investigated whether the damping can also be increased by artificially disordering the topology.
The first step was to identify the parameters of existing additively manufactured lattice structures. The modulus of elasticity, density and damping constants were determined. The identified model was used to build a parameterized FE model of the lattice structures, which enabled an automated adjustment of the topology and the lattice structure. Using heuristic optimization methods, the topology with the highest damping or the highest loss factor could be determined simulatively.
A key result of the investigation is that disorder in the grating can lead to both an increase and a decrease in attenuation. Irregular structures are therefore not per se more damped. In addition, a change in the lattice structure primarily changes the stiffness, which means that the damping itself must always be considered relative to the stiffness. A useful measure for this is the loss factor, which relates the loss work of a period to the deformation energy.
This text was translated with DeepL
Acoustic machine diagnosis of a quartz mill
Duration: 01.05.2022 bis 30.09.2022
This project involved the diagnosis and metrological quantification of the acoustic properties of a permanently operated quartz mill that showed certain abnormalities. The interpretation of the results focused on the question of possible long-term damage and machine failures and thus unplanned downtimes in production.
This text was translated with DeepL
Strength analysis on the frame of a CFRP scooter (kick bike)
Duration: 01.01.2022 bis 30.09.2022
The use of composite structures has long been state of the art in many areas. Due to various factors, however, this is almost never the case for two-wheelers. As part of a model study, various test rigs were therefore set up to analyze the strength properties of the frame of a CFRP scooter (kick bike) in order to derive optimization potential for the composite structure from the results.
The frame was loaded in its main directions and the strains and deformations were measured using various methods. First, optical measurements were taken (using a GOM Aramis system) at several points on the frame in order to determine hotspots of strain and stress in the component. Strain gauges were then applied to these hotspots in order to record the data at the most highly stressed points during the subsequent fracture test and field test with the roller. The fracture test of the scooter frame was carried out at the IKAM technical center in Barleben on a hydraulic punch test bench. As the strains were recorded using strain gauges and optically with the GOM Aramis, measurement errors were eliminated due to data redundancy and the overall quality of the measurement was increased. The strains determined in this way can be used as limit values for use in the field. Another roller was equipped with strain gauges and a data logger so that the strains occurring in the structure during use can be measured.
This makes it possible to determine the degree of utilization and identify oversized areas. Finally, the results of the experimental study can be used to perform a multi-criteria optimization of the structure.
This text was translated with DeepL
Influence of temperature on the frequency-dependent stiffness and damping of elastomer mounts
Duration: 01.05.2022 bis 31.08.2022
Since, in addition to the inertia properties of a structure, it is primarily the stiffness and damping parameters of the bearing that influence its vibration behavior, precise knowledge of these influencing variables is of crucial importance when designing dynamic systems. These parameters are dependent on the vibration frequency and temperature, which must be taken into account for a valid description. Machines that are operated over a long period of time usually heat up, which leads to a drop in damping. Possible consequences are the occurrence of unstable vibrations, the consequences of which can extend to sudden machine failure due to structural or bearing element failure.
A rheological equivalent model can be used to determine an equivalent stiffness and damping resistance at a defined frequency. The energy balance of a full harmonic oscillation of a spring-damper system is used to calculate the parameters, which can then be implemented as characteristic maps in the numerical simulation. The elastomer mounts under investigation are tested using an electrodynamic shaker (max. 440 N sine amplitude), whereby the force between the shaker and the elastomer mount is measured using a piezoelectric load cell (±450N). To determine the deflection, a laser triangulation sensor is used, which records the path between the shaker and the elastomer bearing, from which the force-path relationship follows.
The measurements are carried out for several frequencies under harmonic excitation, whereby the elastomer bearings are also thermally preconditioned with a heating element in the installation position. This allows the dynamic properties to be measured in a small time window after the heating element has been removed.
As a result, various elastomer bearings could be compared in terms of their temperature and frequency-dependent damping (and stiffness), which is very important for use in dynamic machines, as this is the only way to estimate the damping for all operating conditions and identify unstable areas.
This text was translated with DeepL
Comparison of component variants with regard to vibration behavior
Duration: 01.11.2019 bis 31.01.2020
As part of the overall design of machine components, the damping behavior of the structure is of great importance due to its significant impact on noise emissions. As part of the project, the damping effect for two different aluminum alloys is to be investigated on a housing.
The evaluation is based on an experimental vibration analysis using a laser scanning Doppler vibrometer in the entire acoustically perceptible frequency range. The data is provided in both sound and one-third octave bands in order to identify the advantages and disadvantages of each variant.
This text was translated with DeepL
Analysis of the most important design parameters of the piston liner contact w.r.t the accoustic sensitivity
Duration: 01.07.2019 bis 30.11.2019
The acoustic emissions of the combustion engine contribute a main part to the pass by noise of a passenger car, which is the main focus of associated NVH activities.
An adequate simulation model of a crank drive with piston liner contact will be developed. The main bearings and lower con-rod bearings will be modeled as HD-contact, which means hydrodynamic contact without local elasticity. The resulting Reynolds equation will be solved numerically in every step of time integration including all effects due to tilting etc. The crankshaft can be modeled with its global elasticity. The connection from the con-rod to the piston will be modeled using linear stiffness and damping. In later steps this connection can be modeled with the elasticity of the piston pin and hydrodynamic effects. The main focus of the developed model is the piston liner contact modeled as EHD contact, which includes hydrodynamic effects and local elastic deformations of the piston and the cylinder.
After the parameter variation, all variants will be analysed due to the vibration of the crank housing, bearing forces and hydrodynamic condition of the piston linear contact.
Analysis of the most important design parameters of the crank drive w.r.t. the acoustic sensitivity - analysis of influence of the crank shaft design
Duration: 01.07.2019 bis 31.10.2019
The acoustic emissions of the combustion engine contribute a main part to the pass by noise of a passenger car, which is the main focus of associated NVH activities.
Starting from an initial model of the crank shaft at first the CAD data has to be adapted for each variant (given in the analysis matrix). Afterwards an adapted finite element model will be generated including a suitable reduction process. As the setup of the MBS model was realized in previous projects, the adapted crank shafts representations can be implemented directly.
After model setup of all defined variants a nonlinear time integration to the steady state condition for a given speed will be performed. As a result, the bearing forces are present w.r.t. the changed parameters of the crankshaft.
Furthermore the strain energy of the elastic crank shaft model is analysed. The results are averaged (and peak hold) for one load cycle to allow for an overall statement, which regions are sensitive concerning the NVH behavior (due to large strain energy). For reasons of further investigations also the contribution of each eigenmode to the strain energy is calculated and weighted with the participation factor.
After the parameter variation, which is performed in time domain, the bearing forces, which are assumed to affect the NVH behaviour dominantly, are transferred into frequency domain including the resulting phase angle with respect to the crank shaft angle and the different variants are compared.
Simulation of the dynamic behavior of ATL with squeeze oil damper bearings
Duration: 01.04.2019 bis 31.08.2019
The design of the bearings is a key element in the overall design of rotor systems. For cost reasons and due to a large number of advantageous properties, plain bearing elements are predominantly used. However, this is offset by a relatively complex design process, as the movement behavior of the rotor relative to the plain bearings exhibits a highly non-linear behavior. Due to the asymmetrical stiffness and damping properties, self-excited vibrations can occur, which often lead to unstable running of the rotor and are known as oil whirl or oil whip.
In this context, the predictive simulation of rotor behaviour is of key importance in order to minimize cost-intensive prototype tests. In addition, model-based variations of boundary conditions that are difficult to access experimentally, such as the unbalance distribution, can be carried out in order to be able to evaluate the expected vibration behavior a priori.
Since an increase in the degree of modeling is usually accompanied by an increase in computing times and this counteracts the goal of a fast design process, an adequate compromise must be found between the accuracy of the simulation and the resulting effort in the context of the necessary model quality, which also entails parameter variations in modeling.
The aim of the project is to analyze two exhaust gas turbochargers with a different radial bearing concept. While the reference turbocharger is equipped with a semi-floating floating bushing bearing, the new development should manage without a second lubricating film, which is referred to as a compact bearing. The expected vibration behavior and the tribologically relevant bearing parameters in the context of manufacturing tolerances and the transient load must also be investigated, which finally enables an evaluation of the new bearing concept
This text was translated with DeepL
Design of a measuring wheel type for load measurement on an unmodified wheel
Duration: 01.10.2018 bis 28.02.2019
To determine dynamic wheel forces, a measuring method is to be developed that allows the forces to be determined by measuring the load on the rim body. The disadvantages of commercial products are their limited applicability to special vehicles and the need to modify the wheel, in which the rim is split and reconnected using a cylindrical measuring adapter. The force transmitted through the measuring adapter is determined internally by several strain gages and transformed into the stationary system by an angle determined by the external rotary encoder. This method is not practicable for the application under consideration, and there are no suitable measuring adapters in the required size and load range. Therefore, a circular strain measurement is to be carried out on the original rim and the load state in the wheel is to be determined in rotation. Using a suitable rotary encoder (such as the ABS sensor) and an additional reference sensor that determines the absolute position of the wheel, the wheel-fixed load can be transferred to a vehicle-fixed coordinate system.
At the end of the project, a complete measuring wheel with measuring technology will be available. Furthermore, proof of functionality and documentation of the necessary steps for application to the real rim will be provided, whereby the process should be fully scalable.
This text was translated with DeepL
Analysis of the load and stress on a rotary press
Duration: 01.01.2018 bis 30.11.2018
Extrusion is used to manufacture semi-finished products when processing copper. In this process, a pressed part heated to forming temperature is pressed through a die with a punch. In this specific application, heating is achieved by plastic deformation of the raw material on a rotary press. The deflecting friction wheel is fixed via an axial, hydraulically acting clamping device on a shaft that is supported by two roller bearings. A thread is provided for the clamping device in the bearing area, but this shows signs of failure during operation, which is reflected in shearing of the thread flanks and thus a loss of functionality.
In this context, the external loads acting on the machine and thus ultimately on the thread as a result of plastic deformation should first be measured. Due to the forces to be expected, it is not possible to measure the force directly; instead, indirect methods (strain gauges on the counter-holding bracket) must be used.
Once the external loads have been determined, the expected deflection of the shaft structure and the resulting normal bending stresses can be calculated from FE simulations and superimposed with the loads from the hydraulic prestressing to form the nominal total normal stress.
This information on the global stress curve can also be used to analyze the stress distribution in the thread contact using a detailed FE model and to determine the material stress that leads to failure of the structure in the specific application.
This text was translated with DeepL
Simulation of the dynamic behavior of laboratory centrifuges under consideration of the influence of the rotor quick lock
Duration: 01.02.2018 bis 30.06.2018
When designing laboratory centrifuges, in addition to performance parameters such as maximum speed and load, comfort features are also key criteria that have a significant influence on the customer's purchasing decision. One focus here is on high variability of the rotor and the simplest possible changeover. This requirement can be met with quick-locking concepts, although the functionality (connection of shaft and rotor) must be ensured under all circumstances despite simplified use and the dynamic behavior of the overall system, including acoustics, must not deteriorate.
Driven by constant competition and the associated cost pressure, such systems should only incur low additional costs and are therefore usually based on centrifugal force-driven concepts.
An analysis of such systems can be advantageously simulation-based in order to minimize the expected development costs and design modifications.
The aim of the project is to model such a locking mechanism and to test its functionality and the effects on the rotor dynamics on two centrifuges with different rotors and loads. The investigations will then allow an evaluation of the design and, if necessary, adjustments to the targeted design of the product.
This text was translated with DeepL
Analysis of nonlinear rolling bearing dynamics during transient operation as a function of friction and acceleration parameters
Duration: 15.11.2017 bis 31.03.2018
When designing rotor systems with rolling bearings, the design of the bearings is becoming increasingly important. Particularly when non-linear effects such as the load-dependent alternation of rolling and sliding are taken into account, vibration excitations occur which both reduce the service life of the system due to thermal and mechanical loads and cause undesirable noise emissions. By using multi-body models, the mechanical interactions can be mapped in more detail, whereby dynamic effects in transient operation can also be investigated as a result of the general non-linear description in contrast to quasi-stationary approaches.
The aim of the project is to analyze a preloaded angular contact ball bearing with regard to the slip of the rolling elements and the loads on the bearing cage. The main focus is on the influence of the lubricant and thus the friction and acceleration parameters during transient operation. On the basis of the investigations carried out, advantageous combinations are to be derived which, on the one hand, prevent slip-induced heating of the rolling bearing even at high accelerations and, on the other hand, realize a load on the bearing cage below the failure limit.
An improvement in the level of knowledge can be derived from the analysis of the internal cause-effect relationships in the rolling bearing, which also enables a more precise prediction of the non-linear vibration behavior and the associated effects for other applications.
This text was translated with DeepL
Analysis of the dynamical behaviour of turbocharger rotors supported in ball bearings
Duration: 15.03.2017 bis 31.12.2017
Turbochargers are essential elements in the downsizing concept of recent combustion engines. One major development objective is to raise the maximum rotor speed to either increase the air-mass flow or decrease the design size. This causes, among mechanical strength issues, inadequate subsynchronous vibrations known as fluid-whirl and fluid-whip for turbochargers equipped with journal bearings. Another disadvantage of commonly used journal bearings is the rather high friction loss, which is a significant design parameter. To overcome these problems ball bearings concepts are most suitable for advanced designs.
In that context, the simulation of the rotor including the non-linear effects of ball bearings, (with additional squeeze film damper to assure sufficient damping) is essential for an apriori analysis of the system’s dynamics. For that purpose, a dynamic model of the ball bearings including the contact dynamics between the balls, the inner and outer bearing raise and the cage was established and is investigated in detail.
The ball bearings and the squeeze film dampers are implemented with high modelling depth, taking into account all relevant design parameters like initial load, contour of the ball bearings, seals of the squeeze film damper etc.. The system’s eigenbehaviour is investigated using a non-linear and a linearized approach for the stiffness and damping properties of the bearings.
Finally, the results in term of time dependent rotor displacements (under a given rotational frequency of the turbocharger) are examined and compared with measurements to validate the simulation model.
Investigation of the influence of corrosion on the component safety of a rail system for the transportation of mobility-impaired persons
Duration: 01.09.2017 bis 30.11.2017
In ambulances, a rail system is used to secure the mobility-impaired persons to be transported on the vehicle floor, to which the necessary belts are attached. The rails are fixed to a metal sheet and a multiplex plate by means of screw connections via a threaded sleeve whose strength has to be analyzed. The sheet metal is in turn attached to the vehicle floor via an adhesive connection.
To determine the maximum loads on the threaded sleeve, the adjustability of the system and the associated load distribution on the individual fastening elements are modeled as an extreme value problem. The stresses resulting from the maximum loads are then analyzed using adapted FE models. Based on investigations by TÜV Rheinland, a corrosion-induced weakening of the load-bearing cross-section of the threaded sleeve is taken into account and the connection is evaluated with regard to its permissible loads.
This text was translated with DeepL
Measurement of the operating vibrations of a generator
Duration: 01.08.2017 bis 31.10.2017
The frequency response of a generator with innovative air gap development was experimentally recorded as part of the operating vibration analysis in order to characterize the dynamic behaviour. The excitation is carried out as a foot-point excitation with a 10kN shaker, whereby the control was realized via a specially programmed signal generator, which can generate harmonic and non-harmonic signals and regulate them to a defined acceleration amplitude. A sliding sine or sine sweep was used to determine the frequency response. In contrast to conventional methods, which use excitation via impulse hammers, the large excitation forces that can be converted by the shaker also allow non-linear characteristics to be determined, which can occur, for example, as a result of playing fits. As a quintessence, it is thus possible to determine the transmission behavior taking into account the boundary conditions in real operation.
This text was translated with DeepL
Modular battery test bench in the ZTR Roadster
Duration: 01.01.2017 bis 31.10.2017
As part of the project, a ZTR roadster was electrified and designed as a mobile battery test bench. For this purpose, the battery tray was designed in such a way that it can be changed in a short time (approx. 5 minutes). A key element of the new design is the rear swing arm, which was modified to accommodate a permanently excited synchronous motor, which also made it necessary to adapt the transmission ratio of the chain drive to the characteristics of the motor.
In addition to functioning as a mobile battery test bench, the ZTR Roadster offers the opportunity to demonstrate the steps required for electrification from the individual components to the complete vehicle and can be used for media-effective presentation of the work at OVGU in the context of electromobility.
This text was translated with DeepL
Improvement of dynamic behaviour of semi-floating turbocharger with focus on harmonic vibrations
Duration: 01.11.2016 bis 31.03.2017
The aim of the project is a detailed investigation of the non-linear behaviour of a semi-floating turbocharger for the whole operation range. For this task a model is necessary, which describe the eigenbehaviour of the rotor and further include a detailed bearing model as well as a suitable thermal model. In addition the simulations have to be compared with measurements. Finally, suggestions shall be stated to reduce the harmonic vibrations by change of geometrical parameters and by improvement of the balancing process always in the context of resulting friction power and subharmonic vibrations.
Stiffness and damping characterization of rubber buffers
Duration: 01.10.2016 bis 31.03.2017
For the transient simulation of centrifuges, which are often mounted on rubber buffers, the frequency-dependent stiffness and damping properties of the mounting in the three spatial directions represent a significant influence. These properties were measured using a shaker and a force sensor.
For this purpose, the rubber buffers were positioned between a rigid counter bearing and the shaker and subjected to a monofrequency load. The buffer displacement was recorded using a laser vibrometer. With the aid of a force sensor connected in series, the displacement-force diagrams were recorded, from which the stiffness and the degree of damping can be derived. The frequency-dependent rubber buffer characteristics can be determined efficiently by automatically scanning the frequency range.
This text was translated with DeepL
Optimization of turbocharger bearings / rotor dynamics
Duration: 01.07.2014 bis 31.12.2016
During the development process of turbochargers, in addition to the flow and thermodynamic properties, the influences of the rotor dynamics and the design of the bearings are central points that are of great importance. Due to the diverse influences on the vibration behavior, an a priori estimation using simplified formulas is associated with many uncertainties. For this reason, a numerical model of the turbocharger to be developed is to be set up, which maps the rotor dynamic properties including the bearings.
The aim is to study the effects of design changes on subharmonic vibration components (whirl, whip), friction power and bearing forces.
Once a prototype has been implemented, the simulations are to be compared with the measurements carried out and the limiting bearing clearance combinations resulting from the manufacturing accuracy are to be examined with regard to their influence on the vibration behavior.
The work described is carried out analogously for two turbochargers (the design implementations vary as a result of the application in connection with gasoline or diesel engines).
This text was translated with DeepL
Construction and commissioning of a burst test rig for small rotors
Duration: 01.08.2016 bis 01.12.2016
With the aim of investigating the strength properties of miniature rotors, a test rig is to be set up and put into operation that uses laser triangulation sensors to record the expansion of the winding on the rotor and its speed as a function of time. The background to the test rig is the maximum permissible speeds, which are difficult to estimate, especially for fiber-reinforced rotors, before the matrix-fiber connection fails and the rotor is destroyed.
This text was translated with DeepL
Determination of the frequency-dependent stiffness and damping coefficients of the mounting of an exhaust system
Duration: 01.08.2016 bis 01.12.2016
With the aim of investigating the dynamic properties of an exhaust system, the stiffness and damping coefficients of the mount are of great importance in addition to the structural properties of the design, as these have a significant effect on the natural frequencies and thus potential resonance points as well as the expected vibration amplitudes. Due to the elastomer design, there is a frequency dependency of the coefficients, which must be taken into account for a well-founded analysis.
To determine the frequency-dependent stiffness and damping coefficients, a test rig is to be set up and put into operation using laser triangulation sensors and a load cell, which also takes the preload into account via an adapted design. While the bracket is excited with a shaker at a defined frequency , the vibration velocities and the acting forces are recorded in parallel.
After integrating or differentiating the velocity signal, the associated spring stiffness can be calculated knowing the acting force. This information can also be used to determine the hysteresis losses, which can then be used to determine the damping coefficient.
This text was translated with DeepL
Countermeasure suggestions concerning special phenomena of turbochargers
Duration: 01.04.2016 bis 31.08.2016
In the earlier project the influence of different parameter upon harmonic vibrations of a turbocharger rotor has already been analysed. As a result the unbalance distribution and the non-linear characteristics (mainly damping) of the bearings could be identified as significant factors.
The aim of the current project is a further detailed investigation of the system behaviour. For that task a model upgrade concerning eigenfrequencies of the rotor as well as an improved bearing and thermal model are necessary. In addition the simulations have to be compared with measurements. Finally suggestion of countermeasures shall be stated to reduce vibration amplitudes taking into account the current balancing process and the non-linearities of the bearings.
ATL Rotor dynamics simulation
Duration: 01.08.2015 bis 30.06.2016
Based on the knowledge gained in the previous projects "Turbocharger Benchmark" and "Instability of the Turbocharger Bearing" on the simulation of the dynamic behavior of turbochargers, the developed calculation routines are to be applied to another turbocharger. This relates on the one hand to the description of the rotor dynamics of the impeller, taking into account the non-linear bearing, and on the other hand to the reaction on the elastically mapped housing.
Due to a special bearing geometry, axial grooves and profiled bearing supports must be provided. This requires an adaptation of the algorithm with regard to discontinuous gap function curves and the resulting discretization problems.
In this context, parameter variations are performed to predict the effects on the subharmonic oscillations dominating the system behavior and their influences on the rotor dynamics and hydrodynamics.
This text was translated with DeepL
Investigation of turbochargers concerning harmonic vibrations
Duration: 01.01.2016 bis 01.04.2016
During the development of turbochargers one design criterion involves the amplitudes of harmonic and subharmonic vibrations. When using semi-floating bearings often the harmonic vibrations are dominant and have to be reduced in order to get a beneficial acoustic behaviour.
One main influence upon the harmonic vibrations is the unbalance. Assuming a linear system, a reduction of the unbalance will lead to a reduction of the harmonic vibrations especially in the region of the eigenfrequencies.
During some experimental measurements an increase of the amplitudes in the second resonance was observed, although the unbalance of the rotor was decreased.
Beside the unbalance and its distribution also non-linear effects due to the floating ring bearings can be responsible for the described experimental results.
The aim of the project is to investigate the unexpected behaviour using a numerical model of the turbocharger under transient conditions including a non-linear description of the floating ring bearings.
Turbocharger bearing instability
Duration: 01.08.2014 bis 31.07.2015
For the design of turbochargers, it is necessary to describe the harmonic and subharmonic vibrations induced by the non-linear behavior of the floating bushing bearing over the entire operating speed range. The holistic, feedback coupling of rotor dynamics and hydrodynamics must be mapped in order to realize reliable simulation results.
Based on the knowledge gained in the previous project "Turbocharger Benchmark" on the simulation of the dynamic behavior of turbochargers, the developed calculation routines will initially be applied to another turbocharger in order to demonstrate the transferability of the method to other design implementations.
With regard to the comfort criterion "sound emission", a description of the elastic properties of the housing is implemented within the dynamic simulation, whereby the transmission behavior of the disturbance signal caused by the floating bushing bearings to the housing surface is mapped. The transmitted signal is the cause of the sound emission. A comparison with measured surface velocities makes it possible to evaluate the simulation results.
The aim of the project is to provide an improved level of knowledge for the dynamics of turbochargers, especially with regard to the influence of the bearings on maximum speeds, instabilities, service life, etc.
This text was translated with DeepL
Simulation of the rotor dynamics of a kinetic energy storage system
Duration: 01.08.2014 bis 31.12.2014
When designing kinetic (intermediate) energy storage systems, high angular velocities and mass moments of inertia are required to achieve sufficient storage capacities.
This is accompanied by classical questions of rotor dynamics, which primarily concern the inherent behavior and the excitation due to the acting unbalance.
Deviating from the linear considerations, the non-linear, speed-dependent properties of the bearing arrangement, which is implemented here by roller bearings in conjunction with O-rings, must also be taken into account for safety reasons.
In the project, the stiffness and damping characteristics of the O-rings to be used will first be determined experimentally (this also includes investigations of the temperature dependency). In addition, an analysis of the system behavior will be carried out using the determined non-linear properties. The aim is a reliable prediction of the critical speeds including non-linear effects. % (generalized Campbell diagram).
This text was translated with DeepL
Consideration of the dynamic influence of squeeze oil dampers in ADAMS
Duration: 01.07.2014 bis 30.11.2014
Due to the limited speeds of e-turbo units, which are often used in racing, rolling bearing designs are used to minimize friction, which are combined with additional squeeze oil damper elements to achieve sufficient damping values and due to the advantageous thermal properties. In addition to these positive characteristics of the squeeze oil dampers, however, there are also non-linear influences that must be described in combination with the dynamic behavior of the overall system in order to enable a reliable design of the overall system.
Based on the position and velocity vectors of the shaft and shell, the resulting restoring forces, which are determined by Reynolds' differential equation, can be determined. The influence of the Couette flow (shear flow) can be neglected due to the design restriction to purely translational movements of the shaft and shell.
As part of the project, a transient solution to the problem for implementation in ADAMS MSC will be realized using user-written force routines (g-force).
The descriptive differential equation is solved with the aim of an efficient numerical implementation (i.e. using a simplified cavitation algorithm) in the time domain, whereby freely definable oil supply conditions are to be realized.
Parallel to the numerical solution of Reynolds' differential equation, an approximate solution (short-bearing theory) is implemented, whereby initial design processes and the associated parameter studies can be realized with reasonable effort.
This text was translated with DeepL
Run-up simulation II
Duration: 01.10.2011 bis 30.09.2014
The ongoing demand to reduce CO2 emissions and fuel consumption of engines while increasing performance is increasingly leading to downsizing in combination with high-load concepts. Turbochargers can be used to increase the effective mean pressure. In the turbocharger, the exhaust gas energy of the engine is converted into rotational energy by a turbine, which in turn is used to increase the boost pressure of the engine via a compressor. This can significantly increase the efficiency of the overall engine process. From a thermodynamic point of view, the highest possible turbocharger shaft speeds should be aimed for, whereas from a mechanical point of view, these prove to be critical when using plain bearings due to the instabilities that occur. These instabilities are well known as whirl and whip phenomena in rotors mounted in simple radial plain bearings. From a speed nC1, self-excited subharmonic vibrations occur at approximately 0.42 … 0.45 times the rotational frequency with a stable limit cycle (whirl). If this excites a natural frequency of the rotor when the speed is further increased to nC2, this is referred to as whip. The whip frequency remains constant even if the speed is increased further, whereas the bearing becomes unstable and the amplitudes are only limited by the bearing clearance. In order to ensure safe operation beyond nC2, floating bush bearings are used in turbochargers. These are characterized by the fact that the instability occurring on the inner lubricating film is damped by the outer lubricating film and vice versa. This allows the permissible speed range to be increased.
Various efforts have already been made to investigate and expand our understanding of the occurrence of instability (see e.g. FVV - Project Run-up Simulation I ). However, due to the complexity of the topic, further investigation with increased model depth is absolutely necessary to estimate the sensitivities of the influencing parameters. In order to be able to cover the widest possible range of influencing parameters, a numerical solution of the descriptive thermohydroelastic differential equations should be used as a starting point. This means that there are no restrictions, such as those imposed by the use of the impedance method in the FVV - Project Ramp-up Simulation I. Taking into account practicable calculation times for a ramp-up and the results of a systematic DoE study, suitable simplifications must be made within the framework of a permissible mapping quality. The aim of the research project is therefore to reliably map the subharmonic oscillations and instabilities occurring during turbocharger run-up in frequency and amplitude values.
This text was translated with DeepL
Smarter than SMART - Development and simulation of an electrified drivetrain for an electric vehicle conversion (subproject 3)
Duration: 01.07.2011 bis 31.05.2012
In cooperation between the Chairs of Factory Operation and Production Systems at the IAF, the Chair of Design Engineering at the IMK, the Chair of Technical Dynamics at the IFME and the Chair of Mechatronics at the IMS, based on a cooperation with L.E. mobile from Leipzig and coordinated by the Chair of Factory Operation and Production Systems, a purely electric vehicle is being developed as a roadworthy vehicle and an approved test vehicle for long-term use.
This text was translated with DeepL
COmpetence in MObility / Teilbereich A2
Duration: 01.09.2007 bis 31.08.2011
Im Verbundprojekt im Forschungsschwerpunkt Automotive der Otto-von-Guericke Universität Magdeburg wird im Teilbereich A2 das Thema Reibungsreduktion an Tribosystemen bearbeitet. Das Institut für Mechanik (IFME) entwickelt erweiterte Berechnungsmethoden, welche detailierte Aussagen über die Belastung von Gleit- und Wälzlagerungen zulassen. Somit soll die Lebensdauer und die zu erwartende Reibleistung simulativ abgeschätzt werden.
2024
Peer-reviewed journal article
Determination of the mechanical properties of the sacroiliac joint of a dog by imaging measurement methods and model update in a multi-body model
Daniel, Christian; Burkhardt, Sarah; Röhrmann, Nicole; Wagner, Franziska C.; Woschke, Elmar
In: Proceedings in applied mathematics and mechanics - Weinheim : Wiley-VCH . - 2024, Artikel 202400084, insges. 11 S. [Online first]
Optimisation of the hammer throw using parameterised synthetic motion kinematics in a multi‐body simulation
Schmidtchen, Fabian; Daniel, Christian; Tiedemann, Stefan; Woschke, Elmar
In: Proceedings in applied mathematics and mechanics - Weinheim : Wiley-VCH, Bd. 24 (2024), Heft 3, insges. 7 S.
2023
Book chapter
Effectivity of particle dampers with granular filling under rotating conditions
Daniel, Christian; Woschke, Elmar; Prasad, Braj Bhushan; Duvigneau, Fabian
In: Proceedings of SIRM 2023 - the 15th European Conference on Rotordynamics : 22nd - 24th February 2023, Darmstadt, Germany - Darmstadt : TU Darmstadt ; Rinderknecht, Stephan, S. 108-117 [Konferenz: 15th European Conference on Rotordynamics, SIRM 2023, Darmstadt, 22.-24.02.2023]
Hammerwurf-Simulation auf Grundlage von Inertialsensordaten zur Analyse der Wurftechnik
Schmidtchen, Fabian; Tiedemann, Stefan; Daniel, Christian; Witte, Kerstin; Woschke, Elmar
In: dvs-Biomechanik 2023 Tagungsband - Stuttgart : Steinbeis-Edition ; Witte, Kerstin, S. 167-173 [Tagung: dvs-Biomechnik 2023, Magdeburg, 27.-29.09.2023]
Untersuchung der mechanischen und akustischen Emissionen eines elektrischen Gleitboots
Daniel, Christian; Duvigneau, Fabian; Zörnig, Andreas; Woschke, Elmar
In: Aggregate- und Antriebsakustik - 12. Magdeburger Symposium, 28. und 29. Juni 2023 : Tagungsband - Magdeburg : Universitätsbibliothek, Artikel 8, insges. 9 S. [12. Magdeburger Symposium Aggregate- und Antriebsakustik, 2023]
Simulation of foil bearing supported rotor systems
Nitzschke, Steffen; Woschke, Elmar; Daniel, Christian
In: Proceedings of SIRM 2023 - the 15th European Conference on Rotordynamics : 22nd - 24th February 2023, Darmstadt, Germany - Darmstadt : TU Darmstadt ; Rinderknecht, Stephan, S. 257-267 [Konferenz: 15th European Conference on Rotordynamics, SIRM 2023, Darmstadt, 22.-24.02.2023]
Peer-reviewed journal article
Topology optimisation of lattice structures to increase damping
Daniel, Christian; Woschke, Elmar
In: Proceedings in applied mathematics and mechanics - Weinheim : Wiley-VCH, Bd. 22 (2023), Heft 1, Artikel e202200094, insges. 5 S.
Simulation of foil bearing supported rotor systems considering tilting motions
Nitzschke, Steffen; Woschke, Elmar; Daniel, Christian
In: Proceedings in applied mathematics and mechanics - Weinheim : Wiley-VCH, Bd. 23 (2023), Heft 3, Artikel e202300139, insges. 8 S.
2022
Book chapter
Messtechnik zur Verschleißerkennung an Gleichlaufgelenkwellen in Verspannungsprüfständen
Zörnig, Andreas; Daniel, Christian; Schmidt, Hendrik; Woschke, Elmar
In: 1. Fachtagung für Prüfstandsbau und Prüfstandsbetrieb (TestRig) / Fachtagung TestRig , 2022 , 1. Auflage - Tübingen : expert ; Kuttner, Thomas, S. 53-60 [Tagung: 1. Fachtagung TestRig, Esslingen, 22-23.6.2022]
Peer-reviewed journal article
Detection of critical conditions in pouch cells based on their expansion behavior
Vorwerk, Pascal; Hahn, Sarah-Katharina; Daniel, Christian; Krause, Ulrich; Keutel, Karola
In: Batteries - Basel: MDPI, Bd. 8 (2022), 5, insges. 18 S.
Influence of lubricant film cavitation on the vibration behaviour of a semi-floating ring supported turbocharger rotor with thrust bearing
Ziese, Christian; Strackeljan, Cornelius; Nitzschke, Steffen; Daniel, Christian; Woschke, Elmar; Klimpel, Thomas
In: Journal of engineering for gas turbines and power - New York, NY : ASME, Bd. 144 (2022), insges. 19 S.
2021
Book chapter
Gekoppelter Simulationsansatz zur Schwingungsanalyse einer Zentrifuge
Marter, Paul; Daniel, Christian; Duvigneau, Fabian; Woschke, Elmar; Juhre, Daniel
In: Fortschritte der Akustik - DAGA 2021 - Berlin : Deutsche Gesellschaft für Akustik e.V. (DEGA) [Tagung: 47. Jahrestagung für Akustik, DAGA 2021, Wien, 15. bis 18. August 2021]
Rückwirkungsbehaftete gekoppelte Analyse der Elektrodynamik, vibroakustischen Strukturschwingungen und Rotordynamik des elektrischen Antriebsstranges eines Gleitbootes
Duvigneau, Fabian; Koch, Sebastian; Daniel, Christian; Woschke, Elmar; Juhre, Daniel
In: Fortschritte der Akustik - DAGA 2021 - Berlin : Deutsche Gesellschaft für Akustik e.V. (DEGA) [Tagung: 47. Jahrestagung für Akustik, DAGA 2021, Wien, 15. bis 18. August 2021]
Untersuchung unterschiedlicher Modellierungstiefen im Rahmen einer ganzheitlichen Simulationsmethodik zur akustischen Bewertung von Antriebsaggregaten
Nitzschke, Steffen; Duvigneau, Fabian; Daniel, Christian; Juhre, Daniel; Woschke, Elmar
In: Motor- und Aggregate-Akustik - 11. Magdeburger Symposium : Tagungsband [2021] - Magdeburg : Universitätsbibliothek, S. 52-64 [Tagung: Motor- und Aggregate-Akustik : 11. Magdeburger Symposium, 2021]
Detection of wear damage by measuring the strains in ball-constant-velocity joints under operation conditions
Zörnig, Andreas; Daniel, Christian; Schmidt, Hendrik; Woschke, Elmar
In: The 14th International Conference on Dynamics of Rotating Machines , 2021 - Gdańsk : Wydawnictwo IMP PAN ; Żywica, Grzegorz, S. 351-359 [Konferenz: 14th International Conference on Dynamics of Rotating Machines, SIRM 2021, Gdańsk, Poland, February 17-19, 2021]
Transient simulation of a rotor supported in partially filled herringbone grooved journal bearings using the narrow groove theory - boundary conditions
Nitzschke, Steffen; Woschke, Elmar; Daniel, Christian; Sporbeck, Thorsten
In: Vibration Engineering for a Sustainable Future , 1st ed. 2021. - Cham : Springer International Publishing ; Oberst, Sebastian, S. 151-156 - (Numerical and analytical methods to study dynamical systems; Vol. 3)
Transient simulation of a rotor supported in herringbone grooved journal bearings using the narrow groove theory
Nitzschke, Steffen; Woschke, Elmar; Daniel, Christian; Sporbeck, Thorsten
In: Proceedings of 13th SIRM, the 13th International Conference on Dynamics of Rotating Machinery , 2019 - Lyngby, Denmark : Department of Mechanical Engineering, Technical University of Denmark ; Santos, Ilmar Ferreira, S. 150-161 [Konferenz: 13th International Conference on Dynamics of Rotating Machinery, Lyngby, Copenhagen, 13-15 February 2019]
Simulation and measurement of an electric driven turbocharger test rig with full floating ring bearing
Daniel, Christian; Woschke, Elmar; Nitzschke, Steffen
In: Vibration Engineering for a Sustainable Future , 1st ed. 2021. - Cham : Springer International Publishing ; Oberst, Sebastian, S. 3-10
Simulative determination of ideal fluid properties for an automatic ball balancer under different run-up scenarios
Spannan, Lars; Daniel, Christian; Woschke, Elmar
In: Vibration Engineering for a Sustainable Future , 1st ed. 2021. - Cham : Springer International Publishing ; Oberst, Sebastian, S. 3-8 - (Numerical and analytical methods to study dynamical systems; Vol. 3)
Peer-reviewed journal article
Run-up simulation of a semi-floating ring supported turbocharger rotor considering thrust bearing and mass-conserving cavitation
Ziese, Christian; Strackeljan, Cornelius; Nitzschke, Steffen; Daniel, Christian; Woschke, Elmar
In: Lubricants - Basel : MDPI, Bd. 9 (2021), Heft 4, Artikel 44, insges. 23 S.
Consideration of rubber bushings in a multi-body simulation by detailed finite element models
Marter, Paul; Daniel, Christian; Duvigneau, Fabian; Woschke, Elmar; Juhre, Daniel
In: Proceedings in applied mathematics and mechanics - Weinheim [u.a.] : Wiley-VCH, Bd. 21 (2021), Heft 1, Artikel e202100064, insges. 2 S. [Special Issue: 92nd Annual Meeting of the International Association of Applied Mathematics and Mechanics (GAMM)]
2020
Book chapter
Untersuchung des Einflusses von Randbedingungen auf die Vergleichbarkeit von numerischer und experimenteller Modalanalyse
Duvigneau, Fabian; Hähnlein, Frederik; Daniel, Christian; Schrader, Peter; Woschke, Elmar; Juhre, Daniel
In: Fortschritte der Akustik - DAGA 2020 - Berlin : Deutsche Gesellschaft für Akustik e.V. (DEGA), S. 274-277 [Konferenz: DAGA 2020, Hannover, 16.-19. März 2020]
Peer-reviewed journal article
Numerical analysis based on a multi-body simulation for a plunging type constant velocity joint
Marter, Paul; Daniel, Christian; Duvigneau, Fabian; Woschke, Elmar
In: Applied Sciences - Basel : MDPI - Volume 10 (2020), issue 11, article 3715, 18 Seiten
A study on harmonic excitation based experimental characterization of damping materials for acoustic simulations
Spannan, Lars; Duvigneau, Fabian; Gavila Lloret, Maria; Daniel, Christian; Juhre, Daniel; Woschke, Elmar
In: Technische Mechanik - Magdeburg : Inst., Bd. 40 (2020), Heft 2, S. 134-148
2019
Other materials
NVH in der Elektromobilität - Schwingungsanalyse mit Derotator
Duvigneau, Fabian; Daniel, Christian; Koch, Sebastian; Woschke, Elmar
In: Automobiltechnische Zeitschrift - Wiesbaden : Vieweg, Bd. 121 (2019), Heft 6, S. 68-73
Book chapter
Simulation and measurement of ring speed of full floating ring bearing in an automotive turbocharger
Daniel, Christian; Woschke, Elmar; Nitzschke, Steffen
In: Proceedings of 13th SIRM, the 13th International Conference on Dynamics of Rotating Machinery - Lyngby, Denmark : Department of Mechanical Engineering, Technical University of Denmark ; Santos, Ilmar Ferreira . - 2019, S. 142-149 [Konferenz: 13th International Conference on Dynamics of Rotating Machinery, Lyngby, Copenhagen, 13-15 February 2019]
Hochlaufsimulation eines semi-floating gelagerten ATL-Rotors mit schwimmender Axiallagerscheibe
Ziese, Christian; Daniel, Christian; Mostertz, Holger; Woschke, Elmar
In: 14. Magdeburger Maschinenbau-Tage 2019 - Magdeburger Ingenieurtage - 24. und 25. September 2019 : Tagungsband - Magdeburg : Otto von Guericke Universität Magdeburg, Fakultät Maschinenbau, Institut für Mobile Systeme - Lehrstuhl Mechatronik ; Kasper, Roland, S. 105-112 [Tagung: 14 MMT 2019, 24. und 25. September 2019, Magdeburg]
Nutzbarkeitsuntersuchung der Messdaten eines Komponenten-Messrades für die Parameteridentifikation mathematisch-empirischer Reifenmodelle am Beispiel des Forschungsfahrzeugs Editha
Schünemann, Martin; Heidfeld, Hannes; Koch, Sebastian; Daniel, Christian; Kasper, Roland; Woschke, Elmar
In: 14. Magdeburger Maschinenbau-Tage 2019 - Magdeburger Ingenieurtage - 24. und 25. September 2019 : Tagungsband - Magdeburg : Otto von Guericke Universität Magdeburg, Fakultät Maschinenbau, Institut für Mobile Systeme - Lehrstuhl Mechatronik ; Kasper, Roland, S. 47-56 [Tagung: 14 MMT 2019, 24. und 25. September 2019, Magdeburg]
Dynamische Radkraftmessung am PKW im Fahrbetrieb mittels DMS Applikation am Felgenkörper
Daniel, Christian; Woschke, Elmar
In: 14. Magdeburger Maschinenbau-Tage 2019 - Magdeburger Ingenieurtage - 24. und 25. September 2019 : Tagungsband - Magdeburg : Otto von Guericke Universität Magdeburg, Fakultät Maschinenbau, Institut für Mobile Systeme - Lehrstuhl Mechatronik, S. 29-36 [Tagung: 14 MMT 2019, 24. und 25. September 2019, Magdeburg]
Peer-reviewed journal article
Nonlinear vibrations in rotor systems with floating ring bearings induced by fluidstructure interactions
Woschke, Elmar; Nitzschke, Steffen; Daniel, Christian
In: Proceedings in applied mathematics and mechanics - Weinheim [u.a.] : Wiley-VCH, Bd. 19 (2019), Heft 1, insges. 4 S.
NVH in electric mobility - vibration analysis using a derotator
Duvigneau, Fabian; Daniel, Christian; Koch, Sebastian; Woschke, Elmar
In: ATZ worldwide - Wiesbaden : Springer Automotive Media, Bd. 121 (2019), Heft 6, S. 66-71
2018
Book chapter
Vibration analysis of an electric wheel hub motor at stationary operating points
Duvigneau, Fabian; Koch, Sebastian; Daniel, Christian; Woschke, Elmar; Gabbert, Ulrich
In: Proceedings of the 10th International Conference on Rotor Dynamics - IFToMM. Volume 4 - Cham : Springer International Publishing ; Lucchesi Cavalca, Katia . - 2018, S. 51-64 - (Mechanisms and Machine Science; 63) [Konferenz: 10th International Conference on Rotor Dynamics - IFToMM, Rio de Janeiro, Brazil, September 23-27, 2018]
Application of regularised cavitation algorithm for transient analysis of rotors supported in floating ring bearings
Nitzschke, Steffen; Woschke, Elmar; Daniel, Christian
In: Proceedings of the 10th International Conference on Rotor Dynamics - IFToMM. Volume 4 - Cham : Springer International Publishing . - 2018, S. 371-387 - (Mechanisms and Machine Science; 63) [Konferenz: 10th International Conference on Rotor Dynamics - IFToMM, Rio de Janeiro, Brazil, September 23-27, 2018]
Simulation of the ball kinetic in ball-type automatic balancing devices by solving the axisymmetric navier-stokes Equations in annular cavities
Spannan, Lars; Daniel, Christian; Woschke, Elmar
In: Proceedings of the 10th International Conference on Rotor Dynamics - IFToMM. Volume 4 - Cham : Springer International Publishing ; Lucchesi Cavalca, Katia . - 2018, S. 109-118 - (Mechanisms and Machine Science; 63) [Konferenz: 10th International Conference on Rotor Dynamics - IFToMM, Rio de Janeiro, Brazil, September 23-27, 2018]
Peer-reviewed journal article
Design, optimisation and testing of a compact, inexpensive elastic element for series elastic actuators
Irmscher, Cornelius; Woschke, Elmar; May, Erik; Daniel, Christian
In: Medical engineering & physics - Amsterdam [u.a.] : Elsevier Science, Bd. 52 (2018), S. 84-89
Influence of friction-induced heating on the dynamic behaviour of rotors supported by journal bearings
Irmscher, Cornelius; Nitzschke, Steffen; Daniel, Christian; Woschke, Elmar
In: Proceedings in applied mathematics and mechanics - Weinheim : Wiley-VCH - Vol. 18.2018, 1, Art. e201800412 [Special Issue: 89th Annual Meeting of the International Association of Applied Mathematics and Mechanics (GAMM), December 2018]
2017
Book chapter
Simulation rotordynamischer Systeme mit problemangepasster Modellreduktion und erweiterter Modellierungstiefe für Gleit- und Wälzlagerelemente
Daniel, Christian; Woschke, Elmar; Nitzschke, Steffen
In: 13. Magdeburger Maschinenbau-Tage 2017 , 2017 - Magdeburg : Universitätsbibliothek, S. 324-334 [Konferenz: MMT2017]
Entwicklung und Erprobung eines flexiblen Messverfahrens mithilfe FEMgestützter Positionierung von Dehnungsmessstreifen
Koch, Sebastian; Irmscher, Cornelius; Daniel, Christian; Woschke, Elmar
In: 13. Magdeburger Maschinenbau-Tage 2017 , 2017 - Magdeburg : Universitätsbibliothek, S. 171-179 [Konferenz: MMT2017]
Radlastmessung an einem Elektrofahrzeug bei verschiedenen Fahrbahnbelägen inklusive Sonder- und Missbrauchsereignissen
Irmscher, Cornelius; Koch, Sebastian; Daniel, Christian; Woschke, Elmar
In: 13. Magdeburger Maschinenbau-Tage 2017 , 2017 - Magdeburg : Universitätsbibliothek, S. 94-104 [Konferenz: MMT2017]
Peer-reviewed journal article
Experimental study on the velocity dependent drag coefficient and friction in an automatic ball balancer
Spannan, Lars; Daniel, Christian; Woschke, Elmar
In: Technische Mechanik - Magdeburg : Inst., Bd. 37 (2017), Heft 1, S. 62-68
Excitation mechanisms of non-linear rotor systems with floating ring bearings - simulation and validation
Woschke, Elmar; Daniel, Christian; Nitzschke, Steffen
In: International journal of mechanical sciences - Amsterdam [u.a.] : Elsevier Science - 134.2017, Suppl. C, S. 15-27
Dynamic behaviour of EHD-contacts using a regularised, mass conserving cavitation algorithm
Nitzschke, Steffen; Woschke, Elmar; Daniel, Christian
In: Technische Mechanik - Magdeburg : Inst. - Vol. 37.2017, 2-5, S. 181-195
Run-up simulation of automatic balanced rotors considering velocity-dependent drag coefficients
Spannan, Lars; Daniel, Christian; Woschke, Elmar
In: Technische Mechanik - Magdeburg : Inst. - Vol. 37.2017, 2-5, S. 442-449
2016
Book chapter
Simulative analyse of turbine trains under blade fracture conditions with regard to the implementation methods of journal bearings
Woschke, Elmar; Daniel, Christian; Nitzschke, Steffen
In: VIRM 11 - vibrations in rotating machinery / International Conference on Vibrations in Rotating Machinery , 2016 - London : Institution of Mechanical Engineers, S. 431-443 [Kongress: VIRM 11, Manchester, 13-15 September 2016]
An evaluation of computational methods to specify the effects of liquid balancers
Spannan, Lars; Daniel, Christian; Woschke, Elmar; Strackeljan, Jens
In: VIRM 11 - vibrations in rotating machinery / International Conference on Vibrations in Rotating Machinery , 2016 - London : Institution of Mechanical Engineers, S. 785-791 [Kongress: VIRM 11, Manchester, 13-15 September 2016]
2015
Book chapter
Validierung der Hochlaufsimulation für automotive Abgasturbolader
Daniel, Christian; Woschke, Elmar; Nitzschke, Steffen; Strackeljan, Jens; Driot, Nicolas; Braun, Karl-Ludwig; Koutsovasilis, Panagiotis
In: Tagungsbeiträge - Magdeburg, Deutschland, 23. - 25. Februar 2015 / Internationale Tagung Schwingungen in Rotierenden Maschinen , 2015 , Erw. Aufl. - Magdeburg : Institut für Mechanik, Otto von Guericke Universität Magdeburg - 2015, Paper-ID 58, insgesamt 9 S.
DoE basierte Sensitivitätsanalyse konstruktiver Lagerparameter eines gleitgelagerten Abgasturboladers
Göbel, Stefan; Daniel, Christian; Woschke, Elmar; Strackeljan, Jens
In: Tagungsbeiträge - Magdeburg, Deutschland, 23. - 25. Februar 2015 / Internationale Tagung Schwingungen in Rotierenden Maschinen , 2015 , Erw. Aufl. - Magdeburg : Institut für Mechanik, Otto von Guericke Universität Magdeburg - 2015, Paper-ID 55, insgesamt 10 S.
Industrielle Anwendungen der Simulation des Rotationsreibschweißprozesses
Schmicker, David; Kreibich, Marcus; Körner, Markus; Paczulla, Stefan; Daniel, Christian; Jüttner, Sven; Strackeljan, Jens
In: Smart, effizient, mobil - 12. Magdeburger Maschinenbau-Tage ; 30. September und 1. Oktober 2015 , 2015 - Magdeburg : Otto-von-Guericke-Universität Magdeburg - 2015, Art. C3-1 [Kongress: 12. Magdeburger Maschinenbau-Tage, Magdeburg, 30.09. - 01.10. 2015]
Determinismus der subharmonischen Schwingungen in gleitgelagerten Turbomaschinen
Daniel, Christian; Woschke, Elmar; Nitzschke, Steffen; Göbel, Stefan; Strackeljan, Jens
In: Smart, effizient, mobil - 12. Magdeburger Maschinenbau-Tage ; 30. September und 1. Oktober 2015 , 2015 - Magdeburg : Otto-von-Guericke-Universität Magdeburg - 2015, Beitrag A5-2, insgesamt 9 S. Kongress: Magdeburger Maschinenbau-Tage 12 Magdeburg 2015.09.30-10.01
Influence of bearing geometry of automotive turbochargers on the nonlinear vibrations during run-up
Woschke, Elmar; Göbel, Stefan; Nitzschke, Steffen; Daniel, Christian; Strackeljan, Jens
In: Proceedings of the 9th IFToMM International Conference on Rotor Dynamics - Cham : Springer . - 2015, S. 835-844 - (Mechanisms and Machine Science; 21)
Scientific monograph
Hochlaufsimulation II - Nichtlineare Mehrkörpersimulation des Hochlaufverhaltens von Abgasturbolader-Rotoren (ATL-Rotoren) in Schwimmbuchsenlagern unter Verwendung nutzergeschriebener Kraftroutinen innerhalb kommerzieller Mehrkörpersysteme (MKS)$dAbschlussbericht : Vorhaben Nr. 1090 : Beginn der Arbeiten: 01.10.2011 - Ende der Arbeiten: 01.10.2015 : Forschungsvorhaben R 571 (2015)
Daniel, Christian; Woschke, Elmar; Dhrifi, L.; Kraft, Christian; Wetzel, Christian; Driot, N.; Strackeljan, Jens; Schwarze, Hubert; Koutsovasilis, Panagiotis; Lösch-ter Horst, T.
In: Frankfurt am Main: FVV, 2015, IV, 129 Seiten - (Forschungsvereinigung Verbrennungskraftmaschinen e.V.; 1083) [Förderkennzeichen AIF 17288 BG; Ausdruck der Online-Ressource]
2013
Book chapter
Konstruktion, Berechnung und experimentelle Belastungsmessung des Antriebsstranges von Editha
Daniel, Christian; Nitzschke, Steffen; Woschke, Elmar; Strackeljan, Jens
In: Effizienz, Präzision, Qualtität. - Magdeburg : Univ., insges. 9 S., 2013Kongress: Magdeburger Maschinenbau-Tage; 11 (Magdeburg) : 2013.09.25-26
Einfluss der masseerhaltenden Kavitation auf gleitgelagerte Rotoren unter instationärer Belastung
Nitzschke, Steffen; Woschke, Elmar; Daniel, Christian; Strackeljan, Jens
In: Schwingungen in Rotierenden Maschinen. - Berlin : Techn. Univ.; 2013, Paper-ID: ABS-210, insgesamt 11 S.Kongress: SIRM-Tagung; 10 (Berlin) : 2013.02.25-27
Identifikation des Einfluss konstruktiver Lagerparameter eines in Schwimmbuchsen gelagerten Rotorsystems
Daniel, Christian; Nitzschke, Steffen; Woschke, Elmar; Strackeljan, Jens
In: Schwingungen in Rotierenden Maschinen. - Berlin : Techn. Univ.; 2013, Paper-ID: ABS-211, insgesamt 10 S.Kongress: SIRM-Tagung; 10 (Berlin) : 2013.02.25-27
Numerical simulation of the dynamic behaviour of turbochargers under consideration of full-floating-ring bearings and ball bearings
Daniel, Christian; Göbel, Stefan; Nitzschke, Steffen; Woschke, Elmar; Strackeljan, Jens
In: International Conference on Vibration Problems. - Lisboa : APMTAC, insges. 10 S., 2013Kongress: ICOVP; 11 (Lisbon) : 2013.09.09-12
Dissertation
Simulation von gleit- und wälzgelagerten Systemen auf Basis eines Mehrkörpersystems für rotordynamische Anwendungen
Daniel, Christian; Strackeljan, Jens
In: Düsseldorf: VDI-Verl., Zugl.: Magdeburg, Univ., Fak. für Maschinenbau, Diss., 2013, XVIII, 125 S. - (Fortschritt-Berichte VDI; Reihe 11, Schwingungstechnik; 350), ISBN: 978-3-18-335011-7 [Literaturverz. S. 121 - 125][Literaturverz. S. 121 - 125]
2011
Book chapter
Entwicklung von Berechnungsverfahren zur numerischen Simulation des instationären Betriebs von Turboladern
Daniel, Christian; Nitzschke, Steffen; Woschke, Elmar; Strackeljan, Jens
In: Forschung und Innovation - 10. Magdeburger Maschinenbau-Tage ; 27. - 29. September 2011: 10. Magdeburger Maschinenbau-Tage ; 27. - 29. September 2011 - Magdeburg: Univ., 2011; Kasper, Roland . - 2011, insges. 10 S.Kongress: Magdeburger Maschinenbau-Tage 10 (Magdeburg : 2011.09.27-29)
Numerical runup simulation of a turbocharger with full floating ring bearings
Woschke, Elmar; Daniel, Christian; Nitzschke, Steffen; Strackeljan, Jens
In: Vibration problems ICOVP 2011: supplement ; the 10th International Conference on Vibration Problems / tefan Sega ..., ed.: supplement ; the 10th International Conference on Vibration Problems - Liberec: Technical University of Liberec, 2011; Segǐa, Štefan . - 2011, S. 334-339Kongress: ICOVP 10 (Prague : 2011.09.05-08)
Numerische Simulation des instationären Verhaltens der Schwimmbuchsenlagerung in Turboladern
Daniel, Christian; Nitzschke, Steffen; Woschke, Elmar; Strackeljan, Jens
In: Schwingungen in Rotierenden Maschinen - neunte internationale Tagung ; 21. - 23. Februar 2011 Darmstadt, Deutschland ; SIRM 2011 ; Tagungsbeiträte, Proceedings: neunte internationale Tagung ; 21. - 23. Februar 2011 Darmstadt, Deutschland ; SIRM 2011 ; Tagungsbeiträte, Proceedings/ Tagung Schwingungen in Rotierenden Maschinen - neunte internationale Tagung ; 21. - 23. Februar 2011 Darmstadt, Deutschland ; SIRM 2011 ; Tagungsbeiträte, Proceedings - Darmstadt: Techn. Univ., Fachgebiet Strukturdynamik, 2011, 2011, Paper-ID 07, insgesamt 11 S.Kongress: SIRM-Tagung 9 (Darmstadt : 2011.03.21-23)
Original article in peer-reviewed national journal
Simulation von Schwimmbuchsenlagerungen in Abgasturboladern
Nitzschke, Steffen; Woschke, Elmar; Daniel, Christian; Strackeljan, Jens
In: Visnyk Nacionalnogo Techninogo Universytetu Ukraïny "Kyïvskyj Politechninyj Instytut"/ Nacional'nyj techničnyj universytet Ukrainy "Kyivs'kyj politechničnyj instytut" - Kyïv, 2011, Bd. 61.2011, 2, S. 7-12[Ukrainisch-deutsche Konferenz für Maschinenbau "Moderne Werkstoffe und Technologien im Maschinenbau 2011" ; 1 (Kyiv) : 2011.04.13-14]
2010
Book chapter
Simulation von Wälzlagerschäden unter Berücksichtigung von Käfigspiel und Lasteinfluss
Doguer, Tahsin; Tkachuk, Petro; Daniel, Christian; Strackeljan, Jens
In: AKIDA, Aachener Kolloquium für Instandhaltung, Diagnose und Anlagenüberwachung, 17./18. November 2010. - Stolberg : Zillekens - (Aachener Schriften zur Rohstoff- und Entsorgungstechnik des Instituts für Maschinentechnik der Rohstoffindustrie; 73)Kongress: AKIDA; 8 (Aachen) : 2010.11.17-18
Experimentelle und numerische Analyse eines dynamisch belasteten Kurbeltriebs
Daniel, Christian; Woschke, Elmar; Strackeljan, Jens
In: Zylinderlaufbahn, Kolben, Pleuel: innovative Systeme im Vergleich ; 5. VDI-Fachtagung mit Fachausstellung ; Baden-Baden, 07. und 08. Juni 2010 / VDI Werkstofftechnik: innovative Systeme im Vergleich ; 5. VDI-Fachtagung mit Fachausstellung ; Baden-Baden, 07. und 08. Juni 2010 - Düsseldorf: VDI-Verl., 2010 . - 2010, S. 283-296 - (VDI-Berichte; 2109)Kongress: VDI-Fachtagung Zylinderlaufbahn, Kolben, Pleuel: innovative Systeme im Vergleich ; 5. VDI-Fachtagung mit Fachausstellung ; Baden-Baden, 07. und 08. Juni 2010 / VDI Werkstofftechnik 5 (Baden-Baden : 2010.06.07-08)
Peer-reviewed journal article
Experimentelle und numerische Analyse eines dynamisch belasteten Kurbeltriebs
Daniel, Christian; Woschke, Elmar; Strackeljan, Jens
In: VDI-Bericht 2109 - 5. VDI-Fachtagung Zylinderlaufbahn, Kolben, Pleuel, BadenBaden 07.-08.06.2010
2009
Book chapter
Methods to incorporate foundation elasticities in rotordynamic calculations
Ehehalt, Ulrich; Lüneburg, Bernd; Staubach, Reiner; Daniel, Christian; Strackeljan, Jens; Woschke, Elmar
In: Tagungsbeiträge : 23. - 25. Februar 2009, Wien, Österreich // Achte Internationale Tagung Schwingungen in Rotierenden Maschinen. - Wien : Techn. Univ.; 2009, Paper-ID. 41, insges. 10 S.Kongress: SIRM; 8 (Wien) : 2009.02.23-25[Beitrag auf CD-ROM]
Modellierung von Gleitlagern in rotordynamischen Modellen
Daniel, Christian; Strackeljan, Jens; Woschke, Elmar
In: Tagungsbeiträge : 23. - 25. Februar 2009, Wien, Österreich // Achte Internationale Tagung Schwingungen in Rotierenden Maschinen. - Wien : Techn. Univ.; 2009, Paper-ID. 33, insges. 8 S.Kongress: SIRM; 8 (Wien) : 2009.02.23-25[Beitrag auf CD-ROM]
Einbindung thermischer Zustandsvariablen in Mehrkörpersysteme
Woschke, Elmar; Strackeljan, Jens; Daniel, Christian
In: Tagungsbeiträge : 23. - 25. Februar 2009, Wien, Österreich // Achte Internationale Tagung Schwingungen in Rotierenden Maschinen. - Wien : Techn. Univ.; 2009, Paper-ID. 34, insges. 9 S.Kongress: SIRM; 8 (Wien) : 2009.02.23-25[Beitrag auf CD-ROM]
Simulation der Kolbendynamik unter berücksichtigung der EHD-Kopplung
Nitzschke, Steffen; Woschke, Elmar; Daniel, Christian; Strackekjan, Jens
In: Forschung in Bewegung : 9. Magdeburger Maschinenbau-Tage ; 30.09. - 01.10.2009 ; Tagungsband. - Magdeburg : Univ., S. 84-92Kongress: Magdeburger Maschinenbau-Tage; 9 (Magdeburg) : 2009.09.30-10.01
Methoden zur experimentellen und numerischen Analyse dynamisch belasteter Systeme am Beispiel eines Kurbeltriebs
Woschke, Elmar; Daniel, Christian; Schulz, Martin; Strackekjan, Jens
In: Forschung in Bewegung : 9. Magdeburger Maschinenbau-Tage ; 30.09. - 01.10.2009 ; Tagungsband. - Magdeburg : Univ., S. 74-83Kongress: Magdeburger Maschinenbau-Tage; 9 (Magdeburg) : 2009.09.30-10.01
2008
Book chapter
Nutzung von Mehrkörperdynamikprogrammen zur Simulation von Wälzlagerschäden
Strackeljan, Jens; Doguer, Tahsin; Daniel, Christian
In: AKIDA. - Stolberg : Zillekens, 2008 - (Aachener Schriften zur Rohstoff- und Entsorgungstechnik des Instituts für Bergwerks- und Hüttenmaschinenkunde; 70)Kongress: AKIDA; 7 (Aachen) : 2008.11.18-19
Peer-reviewed journal article
Modal approach for consideration of thermal states in multibody systems
Woschke, Elmar; Strackeljan, Jens; Daniel, Christian
In: Proceedings in applied mathematics and mechanics. - Weinheim [u.a.] : Wiley-VCH, Bd. 8.2008, 1, S. 10161-10162
Enhanced fluid bearing simulation with standard multi body systems
Daniel, Christian; Strackeljan, Jens; Woschke, Elmar
In: Proceedings in applied mathematics and mechanics. - Weinheim [u.a.] : Wiley-VCH, Bd. 8.2008, 1, S. 10111-10112
Modal approach for consideration of thermal states in multibody systems
Woschke, Elmar; Strackeljan, Jens; Daniel, Chistian
In: GAMM, 2008, Bremen
Enhanced fluid bearing simulation with standard multi body systems
Daniel, Christian; Strackeljan, Jens; Woschke, Elmar
In: PAMM , Bremen, 2008
2007
Book chapter
Reduktion elastischer Strukturen für MKS Anwendungen
Woschke, Elamr; Daniel, Christian; Strackeljan, Jens
In: AUTOMOTIVE, Impulse für Maschinenbau - 8. Magdeburger Maschinenbau-Tage & 7. MAHREG Innovationsforum, 10. - 11. Oktober 2007 ; Tagungsband - Magdeburg: Univ. . - 2007, S. 187-195Kongress: Magdeburger Maschinenbau-Tage 8 (Magdeburg : 2007.10.10-11)
Reduktion elastischer Strukturen für MKS Anwendungen
Woschke, Elamr; Daniel, Christian; Strackeljan, Jens
In: AUTOMOTIVE, Impulse für Maschinenbau - 8. Magdeburger Maschinenbau-Tage & 7. MAHREG Innovationsforum, 10. - 11. Oktober 2007 ; Tagungsband - Magdeburg : Univ., S. 187-195 Kongress: MAHREG Innovationsforum 7 Magdeburg 2007.10.10-11
Integration von Tribosystemen in MKS-Modelle am Beispiel von Motorkomponenten
Daniel, Christian; Woschke, Elamr; Strackeljan, Jens
In: AUTOMOTIVE, Impulse für Maschinenbau - 8. Magdeburger Maschinenbau-Tage & 7. MAHREG Innovationsforum, 10. - 11. Oktober 2007 ; Tagungsband - Magdeburg : Univ., S. 72-85 Kongress: MAHREG Innovationsforum 7 Magdeburg 2007.10.10-11
Integration von Tribosystemen in MKS-Modelle am Beispiel von Motorkomponenten
Daniel, Christian; Woschke, Elamr; Strackeljan, Jens
In: AUTOMOTIVE, Impulse für Maschinenbau - 8. Magdeburger Maschinenbau-Tage & 7. MAHREG Innovationsforum, 10. - 11. Oktober 2007 ; Tagungsband - Magdeburg: Univ. . - 2007, S. 72-85Kongress: Magdeburger Maschinenbau-Tage 8 (Magdeburg : 2007.10.10-11)
2001-2006 | Studium Maschinenbau Vertiefungsrichtung angewandte Mechanik an der Otto-von-Guericke Universität Magdeburg |
2005-2006 | Hilfswissenschaftler am Institut für Mechanik (IFME) |
2006-2022 | wissenschaftlicher Mittarbeiter am IFME , Lehrstuhl Technische Dynamik (Prof. Dr. habil. J. Strackeljan) |
seit 2022 | wissenschaftlicher Mittarbeiter am IWTM (vorher IFME) , Lehrstuhl Mehrkörperdynamik (Prof. Woschke) |
- Engineering Mechanics 1- exercise ( Link zur LV im LSF )
- Simulation methods of dynamical systems (exercises) ( Link zur LV im LSF )
- Strukturdynamik und Lebensdaueranalyse ( Link zur LV im LSF )
- Strukturdynamik und Lebensdaueranalyse (Übung) ( Link zur LV im LSF )
- Technische Mechanik 3- Hörsaalübung ( Link zur LV im LSF )