Steffen Nitzschke
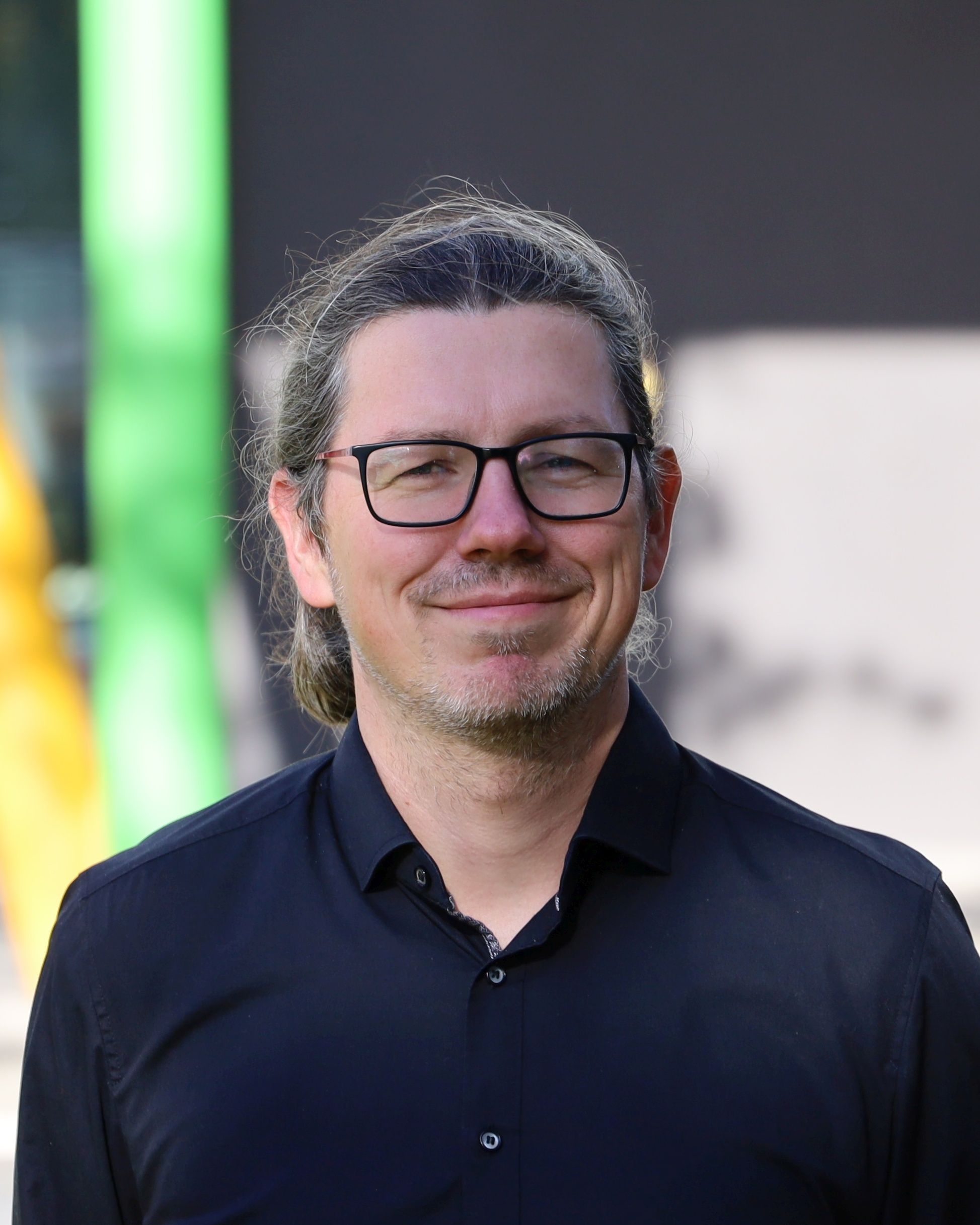
Dr.-Ing. Steffen Nitzschke
Lehrstuhl Mehrkörperdynamik
Completed projects
Vibration analysis of a refrigeration system
Duration: 01.04.2024 bis 31.12.2024
In refrigeration systems, gaseous media are compressed by a compressor and thereby liquefied. The refrigerant is then transported in pipes to other components such as heat exchangers or dryers. The rotary motion of the compressor causes vibration excitation of the pipe system, whereby resonance excitation is also possible depending on the speed and operating point, which can lead to large deformations and system failure, especially in the often weakly damped pipes.
In the project, the vibrations of a piping system are determined experimentally and a 3D FE model of the actual state is created. After validation, design changes in the fastening and mounting of the pipes can be examined for their influence on the stresses acting in the material. Particularly in complex refrigeration systems, the pipelines are very long and angled, which is why an analytical approach is no longer possible.
This development step allows critical pipe vibrations to be determined and suitable design changes to be implemented in the calculation model. In practice, virtual product development saves the construction of prototypes and reduces the final test to a few preferred variants that can be derived from the calculation model.
This text was translated with DeepL
Analysis of the dynamic behavior of rotors in foil bearings
Duration: 01.05.2021 bis 30.11.2023
A key point in the design of rotordynamic systems is the bearing. Compared to conventional bearing concepts such as plain and roller bearings, gas or foil bearings have significantly lower power losses, which is mainly due to the low viscosity and the associated shear stresses of the fluid used (air). As a result of the low viscosity, a low clearance is required to ensure an adequate load carrying capacity. In order to compensate for the temperature rise and the centrifugal force development of the shaft, the bearing shell is designed to allow elastic deformation, which is usually realized by a system of metal foils, e.g. in the form of a top and underlying bump foil. The relative movement between the foils also provides additional damping. During the design process, dynamic simulations of the rotor must be performed to predict the amplitudes due to unbalance and subsynchronous vibrations, the latter defining the stability limit of the system.
The aim of the project is to implement bump-type foil bearings in a rotordynamic simulation in order to be able to perform Campbell diagrams taking into account the non-linearity of the bearings as well as non-linear run-up analyses. The procedure includes an online numerical solution of the Reynolds equation applied to the ideal gas law and combined with different models for the film deformation. A common approach is to use a 1d discretization in the circumferential direction assuming stationary conditions, for which an analytical formulation of the bump film stiffness or a finite element model of the top film is often used. This approach is initially extended to a 2d approach in order to take into account misalignment or tilting of the shaft. To additionally describe the damping of the foil structure in a suitable way, the time-dependent deformation behavior of the foil is mapped, which requires the inclusion of inertial properties and a friction model. This is initially realized by a displacement-dependent structural damping with superimposed Rayleigh damping.
Due to the time dependence, the described formulation leads to further state space equations, which are solved by a Newmark algorithm and are embedded in the time integration of the rotor's equation of motion.
The comparison of the simulation results with the measurements available in the literature shows a high modeling quality of the extended approach, which cannot be realized with quasi-stationary simulations or simplified foil models, resulting in a significant added value in the design of non-linear rotor systems with foil bearings.
This text was translated with DeepL
Influence of axial bearing dynamics on rotor behavior: Transient analysis considering cavitation and the coupling of axial and radial lubrication films
Duration: 01.01.2020 bis 31.05.2021
In addition to the elastic and inertia properties of the rotor and the external loads, the vibration behavior of rotor systems is primarily determined by the bearing. Due to the advantageous mechanical and thermal characteristics as well as the low costs, plain bearing designs are often used. On the one hand, this applies to radial plain bearings, which have a dominant influence on bending vibrations; at the same time, axial plain bearings are used for axial securing or for absorbing axial loads. Due to their respective stiffness and damping parameters, both bearing types make a significant contribution to system behavior, which has a drastic effect on the resulting vibrations and stability. Continuous further developments and increasing requirements require a successively higher mapping quality of the transient system behavior, which is why detailed modeling of the system properties of the rotor system, the bearing and their interactions is necessary.
For transient investigations, the use of established quasi-stationary solutions in the field of coupled rotor-bearing simulation is not adequately possible. While the solution of a non-linear system of equations is sufficient for quasi-stationary considerations of the bearing situation, time integrations must be carried out for transient questions, taking into account the rotor dynamics. A correspondingly detailed representation of the bearing situation requires the evaluation of Reynolds' differential equation in each step of the time integration, taking into account the time-variant cavitation state.
In the previous project, a modified cavitation algorithm according to Elrod was developed for radial bearings, which is now to be transferred to axial bearings. In this context, in addition to the simple thrust bearing, there are various other designs that can be divided into combined bearings (radial/axial composite plain bearings), floating disk bearings and tilting pad bearings. Hydraulic couplings between axial and radial lubrication films as well as mechanical couplings to the components of the rotor-bearing system under the influence of cavitation must be taken into account. With the extended simulation model, relevant vibration phenomena (subharmonic vibrations, counter-rotation excitations due to external loads, tilting pad vibrations) are to be validly predicted in terms of frequency and amplitude.
This text was translated with DeepL
Numerical analysis of the transient behavior of dynamically loaded rotor systems in plain and floating bushing bearings under consideration of cavitative effects
Duration: 01.09.2016 bis 31.08.2019
The aim of the project is to improve the mapping quality of rotor systems with plain and floating bush bearings, taking into account high speeds and variable dynamic loads. A particular focus is on the mapping of transient effects, which can have a massive influence on the system behavior.
For the consideration of these problems, there is no generally valid approach that includes the non-linear effects of the hydrodynamic bearings in the time domain, taking into account a mass-conserving cavitation algorithm. The binary behaviour of the discretization, which is necessary for the solution of the descriptive Reynolds differential equation (assignment is either to the cavitation or to the pressure region), is to be regularized in order to improve on the current status. This means that individual elements can be part of both the cavitation and pressure domains, enabling a continuous transition independent of the elementization.
While pure plain bearing concepts are often used for technical applications with moderate speeds, concepts with floating bush bearings are largely used in the high speed range, whose tendency to subharmonic vibrations is to be investigated in connection with rotordynamic issues and the cavitation algorithm to be regularized.
The project offers the opportunity to increase system understanding in the simulation of rotor systems with sliding and floating bush bearings. Due to the absolutely stable convergence properties of the extended modeling method, a transient investigation of the mechanical system including all dominant hydrodynamic effects can be implemented.
This text was translated with DeepL
Nonlinear vibration simulation of a differential gearbox
Duration: 01.08.2018 bis 28.02.2019
When designing differential gearboxes, acoustic behavior is a quality criterion in addition to pure functionality and high efficiency. Due to the large number of moving elements, their contacts with each other and the non-linear bearing properties, the multi-criteria design of the construction is usually only possible using numerical simulations and accompanying experimental investigations.
As part of the simulation, which can be advantageously implemented using multi-body systems due to the large reference movements, the excitation mechanisms on the one hand and the non-linear behavior of the overall system due to the plain bearing on the other must be correctly mapped. Significant influences arise from the elastic properties of the individual components and the behavior of the bearing. The latter is not trivial, especially for the thrust washer composite of the bevel gears, as spherical plain bearings with additional plastic elements are used here. A detailed mapping of the stiffness and damping influences as part of the overall simulation of the system behavior finally allows a holistic assessment of the design.
This text was translated with DeepL
Analysis of the most important design parameters of the crank drive due to the NVH behaviour - analysis of the main bearing forces w.r.t. the acoustic sensitivity
Duration: 01.04.2018 bis 30.11.2018
The acoustic emissions of the combustion engine are one of the main contributors to the pass by noise of a passenger car, which is a main focus of current NVH activities.
In this context the crank drive has a dominant influence and has to be analyzed in detail to identify the most important design parameters concerning vibrations of the main bearings, which defines one excitation source of the engine's acoustic emission. Thereby, the main focus will be on design parameters, which can easily be changed in an already existing production line for mass production of passenger cars.
The deformation of the crank shaft, which was calculated with the previously defined MBS model under nominal conditions (two rotational speeds) is analyzed concerning the strain energy. The results are averaged for one load cycle to allow for an overall statement, which regions are sensitive concerning the NVH behavior (due to large strain energy). This approach neglects the non-linear interactions between the vibration behaviour of the crank shaft and the bearing parameter, but it allows for a determination of relevant geometrical parameters of the crank shaft. For reasons of further investigations also the contribution of each eigenmode to the strain energy is calculated and weighted with the participation factor.
After a parameter variation, which is performed in time domain, the bearing forces, which are assumed to affect the NVH behaviour dominantly, are transferred into frequency domain including the resulting phase angle with respect to the crank shaft angle. Furthermore, acoustic sensitivities for each bearing (from experimental or computational data) are used to compare different variants. In this context several aspects has to be taken into account: On the one hand vibration with different opposed phases vanish (phase cancel). On the other hand high bearing forces, which result from eigenvalues in the interesting frequency domain, can be shifted towards frequencies with low acoustic sensitivities, leading to a lower sound pressure (eigenvalue dispersion). The last point to mention is a mode control, so that specific modes are tuned to assure that the amplitudes in the bearings tend to zero.
Transient axial bearing simulation under consideration of mass-preserving cavitation
Duration: 01.11.2016 bis 31.03.2018
In addition to the radial bearings of rotors, their axial bearings also play an important role in the design of rotordynamic systems. Two thrust bearings acting against each other - the main bearing and the auxiliary bearing - are used for this purpose, particularly in the case of low or alternating axial loads. Due to the larger axial gap, the auxiliary bearing in particular is only partially filled, which results in lower frictional power compared to a fully filled bearing. Under transient conditions, the filling levels of both gaps depend on time and load and thus lead to variable pressure distributions in the segments and also to varying stiffness and damping properties of the overall bearing.
The aim of this project is therefore to simulate the described transient behavior and integrate it into a rotor dynamics model. The cavitation behaviour is implemented on the one hand based on a regularized variant of the Elrod algorithm and on the other hand using the two-phase model. First, a validation or verification under static loads is sought before corresponding transient investigations are carried out.
This text was translated with DeepL
Analysis of the most important design parameters of the crank drive due to the NVH behaviour - Analysis of the crank shaft and the main bearings
Duration: 01.11.2017 bis 28.02.2018
The acoustic emissions of the combustion engine are one of the main contributors to the pass by noise of a passenger car, which is a main focus of current NVH activities.
In this context the crank drive has a dominant influence and has to be analyzed in detail to identify the most important design parameters concerning vibrations of the main bearings, which defines one excitation source of the engine's acoustic emission. Thereby, the main focus will be on design parameters, which can easily be changed in an already existing production line for mass production of passenger cars. For this purpose a multi-body-simulation model of the crank drive is build.
Beside the crankshaft, which will be modeled as an elastic body (using the floating frame of reference approach - elastic deformations are superimposed to the rigid body motion via a reduced FE-model), the remaining bodies are assumed as rigid. The bearings on the crank shaft are modeled by a transient solution of Reynolds PDE, which allows a detailed analysis of the bearing forces and the influence of bearing parameters. The exciting forces are determined by the transient combustion forces acting on the pistons. As it is assumed that a lower magnitude of excitation forces leads to lower acoustic emissions, the numerical results of interest are the forces in the main bearings, which can excite the crankcase and lead to a noticeable acoustic behaviour.
Simulation of ATL with dual-volute charging
Duration: 15.10.2017 bis 31.01.2018
In addition to the conventional working principle of ram charging, the turbine of an exhaust gas turbocharger can alternatively be operated by means of shock charging. This variant utilizes not only the pressure differences across the turbine but also the kinetic energy of the exhaust gas, which results in efficiency advantages. However, due to the pulsating pressure in the exhaust gas, this leads to a transiently changing output torque of the turbine, which can result in vibrations of the impeller on the one hand and a change in run-up characteristics on the other. The specific effects on the rotordynamic behavior have not yet been conclusively investigated due to the strong non-linearity of the system behavior.
In this project, the influence of shock charging compared to conventional ram charging is investigated with regard to the rotor dynamics of the rotor and its radial bearing, which is designed as a floating bushing bearing. Adequate modeling of the bearing properties, which must reliably map typical non-linear effects such as oil whirl and oil whip in frequency and amplitude, is of essential importance, from which statements regarding the influence of the bearing on maximum speeds, instabilities, service life, etc. can be derived.
This text was translated with DeepL
Investigation of the influence of corrosion on the component safety of a rail system for the transportation of mobility-impaired persons
Duration: 01.09.2017 bis 30.11.2017
In ambulances, a rail system is used to secure the mobility-impaired persons to be transported on the vehicle floor, to which the necessary belts are attached. The rails are fixed to a metal sheet and a multiplex plate by means of screw connections via a threaded sleeve whose strength has to be analyzed. The sheet metal is in turn attached to the vehicle floor via an adhesive connection.
To determine the maximum loads on the threaded sleeve, the adjustability of the system and the associated load distribution on the individual fastening elements are modeled as an extreme value problem. The stresses resulting from the maximum loads are then analyzed using adapted FE models. Based on investigations by TÜV Rheinland, a corrosion-induced weakening of the load-bearing cross-section of the threaded sleeve is taken into account and the connection is evaluated with regard to its permissible loads.
This text was translated with DeepL
Optimization of turbocharger bearings / rotor dynamics
Duration: 01.07.2014 bis 31.12.2016
During the development process of turbochargers, in addition to the flow and thermodynamic properties, the influences of the rotor dynamics and the design of the bearings are central points that are of great importance. Due to the diverse influences on the vibration behavior, an a priori estimation using simplified formulas is associated with many uncertainties. For this reason, a numerical model of the turbocharger to be developed is to be set up, which maps the rotor dynamic properties including the bearings.
The aim is to study the effects of design changes on subharmonic vibration components (whirl, whip), friction power and bearing forces.
Once a prototype has been implemented, the simulations are to be compared with the measurements carried out and the limiting bearing clearance combinations resulting from the manufacturing accuracy are to be examined with regard to their influence on the vibration behavior.
The work described is carried out analogously for two turbochargers (the design implementations vary as a result of the application in connection with gasoline or diesel engines).
This text was translated with DeepL
Friction power simulation oil pump
Duration: 01.06.2015 bis 31.01.2016
As part of technology optimization and cost minimization, sensors whose measurement data is also available for indirect determination are to be eliminated.
In this context, experimental studies have shown unexpected changes in friction performance depending on various parameters in certain constructive implementations of an oil pump.
A description of the dynamic behavior, including the hydrodynamic conditions and thus the resulting forces in the pump, is essential for investigating the mechanisms of action. For this reason, a hydrodynamic-mechanical coupled MBS model of the pump is set up and a simulative study is carried out depending on the design parameters.
In addition, the resulting loads make it possible to assess the load-bearing capacity of the main bearing.
This text was translated with DeepL
Run-up simulation II
Duration: 01.10.2011 bis 30.09.2014
The ongoing demand to reduce CO2 emissions and fuel consumption of engines while increasing performance is increasingly leading to downsizing in combination with high-load concepts. Turbochargers can be used to increase the effective mean pressure. In the turbocharger, the exhaust gas energy of the engine is converted into rotational energy by a turbine, which in turn is used to increase the boost pressure of the engine via a compressor. This can significantly increase the efficiency of the overall engine process. From a thermodynamic point of view, the highest possible turbocharger shaft speeds should be aimed for, whereas from a mechanical point of view, these prove to be critical when using plain bearings due to the instabilities that occur. These instabilities are well known as whirl and whip phenomena in rotors mounted in simple radial plain bearings. From a speed nC1, self-excited subharmonic vibrations occur at approximately 0.42 … 0.45 times the rotational frequency with a stable limit cycle (whirl). If this excites a natural frequency of the rotor when the speed is further increased to nC2, this is referred to as whip. The whip frequency remains constant even if the speed is increased further, whereas the bearing becomes unstable and the amplitudes are only limited by the bearing clearance. In order to ensure safe operation beyond nC2, floating bush bearings are used in turbochargers. These are characterized by the fact that the instability occurring on the inner lubricating film is damped by the outer lubricating film and vice versa. This allows the permissible speed range to be increased.
Various efforts have already been made to investigate and expand our understanding of the occurrence of instability (see e.g. FVV - Project Run-up Simulation I ). However, due to the complexity of the topic, further investigation with increased model depth is absolutely necessary to estimate the sensitivities of the influencing parameters. In order to be able to cover the widest possible range of influencing parameters, a numerical solution of the descriptive thermohydroelastic differential equations should be used as a starting point. This means that there are no restrictions, such as those imposed by the use of the impedance method in the FVV - Project Ramp-up Simulation I. Taking into account practicable calculation times for a ramp-up and the results of a systematic DoE study, suitable simplifications must be made within the framework of a permissible mapping quality. The aim of the research project is therefore to reliably map the subharmonic oscillations and instabilities occurring during turbocharger run-up in frequency and amplitude values.
This text was translated with DeepL
2023
Book chapter
Simulation of foil bearing supported rotor systems
Nitzschke, Steffen; Woschke, Elmar; Daniel, Christian
In: Proceedings of SIRM 2023 - the 15th European Conference on Rotordynamics : 22nd - 24th February 2023, Darmstadt, Germany - Darmstadt : TU Darmstadt ; Rinderknecht, Stephan, S. 257-267 [Konferenz: 15th European Conference on Rotordynamics, SIRM 2023, Darmstadt, 22.-24.02.2023]
Peer-reviewed journal article
Simulation of foil bearing supported rotor systems considering tilting motions
Nitzschke, Steffen; Woschke, Elmar; Daniel, Christian
In: Proceedings in applied mathematics and mechanics - Weinheim : Wiley-VCH, Bd. 23 (2023), Heft 3, Artikel e202300139, insges. 8 S.
Nonlinear vibration phenomena in hydrodynamically supported rotor systems
Nitzschke, Steffen; Woschke, Elmar; Strackeljan, Cornelius
In: GAMM-Mitteilungen / Gesellschaft für Angewandte Mathematik und Mechanik - Weinheim : Wiley-VCH . - 2023, insges. 21 S. [Online first]
2022
Peer-reviewed journal article
Influence of lubricant film cavitation on the vibration behaviour of a semi-floating ring supported turbocharger rotor with thrust bearing
Ziese, Christian; Strackeljan, Cornelius; Nitzschke, Steffen; Daniel, Christian; Woschke, Elmar; Klimpel, Thomas
In: Journal of engineering for gas turbines and power - New York, NY : ASME, Bd. 144 (2022), insges. 19 S.
2021
Book chapter
Run-up simulation of a floating ring supported turbocharger rotor with thrust bearing considering mass-conserving cavitation
Ziese, Christian; Strackeljan, Cornelius; Nitzschke, Steffen; Woschke, Elmar
In: The 14th International Conference on Dynamics of Rotating Machines , 2021 - Gdańsk : Wydawnictwo IMP PAN, S. 134-144 [Konferenz: 14th International Conference on Dynamics of Rotating Machines, SIRM 2021, Gdańsk, Poland, February 17-19, 2021]
Transient simulation of a rotor supported in herringbone grooved journal bearings using the narrow groove theory
Nitzschke, Steffen; Woschke, Elmar; Daniel, Christian; Sporbeck, Thorsten
In: Proceedings of 13th SIRM, the 13th International Conference on Dynamics of Rotating Machinery , 2019 - Lyngby, Denmark : Department of Mechanical Engineering, Technical University of Denmark ; Santos, Ilmar Ferreira, S. 150-161 [Konferenz: 13th International Conference on Dynamics of Rotating Machinery, Lyngby, Copenhagen, 13-15 February 2019]
Simulation and measurement of an electric driven turbocharger test rig with full floating ring bearing
Daniel, Christian; Woschke, Elmar; Nitzschke, Steffen
In: Vibration Engineering for a Sustainable Future , 1st ed. 2021. - Cham : Springer International Publishing ; Oberst, Sebastian, S. 3-10
Untersuchung unterschiedlicher Modellierungstiefen im Rahmen einer ganzheitlichen Simulationsmethodik zur akustischen Bewertung von Antriebsaggregaten
Nitzschke, Steffen; Duvigneau, Fabian; Daniel, Christian; Juhre, Daniel; Woschke, Elmar
In: Motor- und Aggregate-Akustik - 11. Magdeburger Symposium : Tagungsband [2021] - Magdeburg : Universitätsbibliothek, S. 52-64 [Tagung: Motor- und Aggregate-Akustik : 11. Magdeburger Symposium, 2021]
Analysis of dynamical behaviour of rotors under axial loads and supported by full-floating disk thrust bearing
Nitzschke, Steffen; Ziese, Christian; Woschke, Elmar
In: The 14th International Conference on Dynamics of Rotating Machinery / International Conference on Dynamics of Rotating Machines , 2021 - Gdańsk, Poland : Institute of Fluid Flow Machinery, Polish Academy of Science ; Żywica, Grzegorz, S. 72-81 [Konferenz: 14th International Conference on Dynamics of Rotating Machines, SIRM 2021, Gdańsk, Poland, February 17-19, 2021]
Transient simulation of a rotor supported in partially filled herringbone grooved journal bearings using the narrow groove theory - boundary conditions
Nitzschke, Steffen; Woschke, Elmar; Daniel, Christian; Sporbeck, Thorsten
In: Vibration Engineering for a Sustainable Future , 1st ed. 2021. - Cham : Springer International Publishing ; Oberst, Sebastian, S. 151-156 - (Numerical and analytical methods to study dynamical systems; Vol. 3)
Peer-reviewed journal article
Run-up simulation of a semi-floating ring supported turbocharger rotor considering thrust bearing and mass-conserving cavitation
Ziese, Christian; Strackeljan, Cornelius; Nitzschke, Steffen; Daniel, Christian; Woschke, Elmar
In: Lubricants - Basel : MDPI, Bd. 9 (2021), Heft 4, Artikel 44, insges. 23 S.
Modelling the dynamic contact forces during orthogonal turn-milling
Knape, Katharina; Nitzschke, Steffen; Woschke, Elmar
In: Proceedings in applied mathematics and mechanics - Weinheim [u.a.] : Wiley-VCH, Bd. 21 (2021), Heft 1, Artikel e202100056 [Special Issue: 92nd Annual Meeting of the International Association of Applied Mathematics and Mechanics (GAMM)]
Analysis of dynamical behaviour of full-floating disk thrust bearings
Nitzschke, Steffen; Ziese, Christian; Woschke, Elmar
In: Bulletin of the Polish Academy of Sciences / Technical sciences / Polska Akademia Nauk - Warsaw : PAS, Division IV Technical Sciences . - 2021, insges. 10 S. [Online first]
2020
Peer-reviewed journal article
Run up simulation of a full-floating ring supported Jeffcott-rotor considering two-phase flow cavitation
Ziese, Christian; Nitzschke, Steffen; Woschke, Elmar
In: Archive of applied mechanics - Berlin : Springer, Bd. 91 (2021), S. 777-790
2019
Book chapter
Simulation and measurement of ring speed of full floating ring bearing in an automotive turbocharger
Daniel, Christian; Woschke, Elmar; Nitzschke, Steffen
In: Proceedings of 13th SIRM, the 13th International Conference on Dynamics of Rotating Machinery - Lyngby, Denmark : Department of Mechanical Engineering, Technical University of Denmark ; Santos, Ilmar Ferreira . - 2019, S. 142-149 [Konferenz: 13th International Conference on Dynamics of Rotating Machinery, Lyngby, Copenhagen, 13-15 February 2019]
Transient thermo-hydrodynamic analysis of a laval rotor supported by journal bearings with respect to calculation times
Irmscher, Cornelius; Nitzschke, Steffen; Woschke, Elmar
In: Proceedings of 13th SIRM, the 13th International Conference on Dynamics of Rotating Machinery - Lyngby, Denmark : Department of Mechanical Engineering, Technical University of Denmark ; Santos, Ilmar Ferreira . - 2019, S. 162-173 [Konferenz: 13th International Conference on Dynamics of Rotating Machinery, Lyngby, Copenhagen, 13-15 February 2019]
Peer-reviewed journal article
Nonlinear vibrations in rotor systems with floating ring bearings induced by fluidstructure interactions
Woschke, Elmar; Nitzschke, Steffen; Daniel, Christian
In: Proceedings in applied mathematics and mechanics - Weinheim [u.a.] : Wiley-VCH, Bd. 19 (2019), Heft 1, insges. 4 S.
2018
Book chapter
Application of regularised cavitation algorithm for transient analysis of rotors supported in floating ring bearings
Nitzschke, Steffen; Woschke, Elmar; Daniel, Christian
In: Proceedings of the 10th International Conference on Rotor Dynamics - IFToMM. Volume 4 - Cham : Springer International Publishing . - 2018, S. 371-387 - (Mechanisms and Machine Science; 63) [Konferenz: 10th International Conference on Rotor Dynamics - IFToMM, Rio de Janeiro, Brazil, September 23-27, 2018]
Peer-reviewed journal article
Influence of friction-induced heating on the dynamic behaviour of rotors supported by journal bearings
Irmscher, Cornelius; Nitzschke, Steffen; Daniel, Christian; Woschke, Elmar
In: Proceedings in applied mathematics and mechanics - Weinheim : Wiley-VCH - Vol. 18.2018, 1, Art. e201800412 [Special Issue: 89th Annual Meeting of the International Association of Applied Mathematics and Mechanics (GAMM), December 2018]
2017
Book chapter
Simulation rotordynamischer Systeme mit problemangepasster Modellreduktion und erweiterter Modellierungstiefe für Gleit- und Wälzlagerelemente
Daniel, Christian; Woschke, Elmar; Nitzschke, Steffen
In: 13. Magdeburger Maschinenbau-Tage 2017 , 2017 - Magdeburg : Universitätsbibliothek, S. 324-334 [Konferenz: MMT2017]
Tragdruck- und Schmierstoffverteilung von Axialgleitlagern unter Berücksichtigung von masseerhaltender Kavitation und Zentrifugalkraft
Ziese, Christian; Woschke, Elmar; Nitzschke, Steffen
In: 13. Magdeburger Maschinenbau-Tage 2017 , 2017 - Magdeburg : Universitätsbibliothek, S. 312-323 [Konferenz: MMT2017]
Peer-reviewed journal article
Dynamic behaviour of EHD-contacts using a regularised, mass conserving cavitation algorithm
Nitzschke, Steffen; Woschke, Elmar; Daniel, Christian
In: Technische Mechanik - Magdeburg : Inst. - Vol. 37.2017, 2-5, S. 181-195
Excitation mechanisms of non-linear rotor systems with floating ring bearings - simulation and validation
Woschke, Elmar; Daniel, Christian; Nitzschke, Steffen
In: International journal of mechanical sciences - Amsterdam [u.a.] : Elsevier Science - 134.2017, Suppl. C, S. 15-27
2016
Book chapter
Simulative analyse of turbine trains under blade fracture conditions with regard to the implementation methods of journal bearings
Woschke, Elmar; Daniel, Christian; Nitzschke, Steffen
In: VIRM 11 - vibrations in rotating machinery / International Conference on Vibrations in Rotating Machinery , 2016 - London : Institution of Mechanical Engineers, S. 431-443 [Kongress: VIRM 11, Manchester, 13-15 September 2016]
Peer-reviewed journal article
A holistic approach for the vibration and acoustic analysis of combustion engines including hydrodynamic interactions
Duvigneau, Fabian; Nitzschke, Steffen; Woschke, Elmar; Gabbert, Ulrich
In: Archive of applied mechanics - Berlin : Springer . - 2016, insges. 14 S.
Regularised cavitation algorithm for use in transient rotordynamic analysis
Nitzschke, Steffen; Woschke, Elmar; Schmicker, David; Strackeljan, Jens
In: International journal of mechanical sciences - Amsterdam [u.a.] : Elsevier Science, Bd. 113 (2016), S. 175-183
Dissertation
Instationäres Verhalten schwimmbuchsengelagerter Rotoren unter Berücksichtigung masseerhaltender Kavitation
Nitzschke, Steffen; Woschke, Elmar; Strackeljan, Jens
In: Clausthal-Zellerfeld: Papierflieger Verlag, 2017, Dissertation Otto-von-Guericke-Universität Magdeburg, Fakultät für Maschinenbau 2016, XVIII, 151 Seiten, ISBN: 978-3-86948-553-9 [Literaturverzeichnis: Seite 140-149][Literaturverzeichnis: Seite 140-149]
2015
Book chapter
Influence of bearing geometry of automotive turbochargers on the nonlinear vibrations during run-up
Woschke, Elmar; Göbel, Stefan; Nitzschke, Steffen; Daniel, Christian; Strackeljan, Jens
In: Proceedings of the 9th IFToMM International Conference on Rotor Dynamics - Cham : Springer . - 2015, S. 835-844 - (Mechanisms and Machine Science; 21)
Validierung der Hochlaufsimulation für automotive Abgasturbolader
Daniel, Christian; Woschke, Elmar; Nitzschke, Steffen; Strackeljan, Jens; Driot, Nicolas; Braun, Karl-Ludwig; Koutsovasilis, Panagiotis
In: Tagungsbeiträge - Magdeburg, Deutschland, 23. - 25. Februar 2015 / Internationale Tagung Schwingungen in Rotierenden Maschinen , 2015 , Erw. Aufl. - Magdeburg : Institut für Mechanik, Otto von Guericke Universität Magdeburg - 2015, Paper-ID 58, insgesamt 9 S.
Virtual engineering approach for the acoustic behavior of an engine
Duvigneau, Fabian; Nitzschke, Steffen; Strackeljan, Jens; Gabbert, Ulrich
In: The 22nd International Congress on Sound and Vibration, ICSV 22 - Florence - 2015, Session T13.RS07, Paper 536 [Kongress: 22nd International Congress on Sound and Vibration, ICSV 22, Florence, Italy, 12 - 16 July 2015]
Determinismus der subharmonischen Schwingungen in gleitgelagerten Turbomaschinen
Daniel, Christian; Woschke, Elmar; Nitzschke, Steffen; Göbel, Stefan; Strackeljan, Jens
In: Smart, effizient, mobil - 12. Magdeburger Maschinenbau-Tage ; 30. September und 1. Oktober 2015 , 2015 - Magdeburg : Otto-von-Guericke-Universität Magdeburg - 2015, Beitrag A5-2, insgesamt 9 S. Kongress: Magdeburger Maschinenbau-Tage 12 Magdeburg 2015.09.30-10.01
Ganzheitlicher Virtual Engineering Ansatz zur Schwingungs- und Akustiksimulation eines Verbrennungsmotors
Duvigneau, Fabian; Nitzschke, Steffen; Strackeljan, Jens; Gabbert, Ulrich
In: Tagungsbeiträge - Magdeburg, Deutschland, 23. - 25. Februar 2015 / Internationale Tagung Schwingungen in Rotierenden Maschinen , 2015 , Erw. Aufl. - Magdeburg : Institut für Mechanik, Otto von Guericke Universität Magdeburg - 2015, Paper-ID 61, insgesamt 11 S.
Peer-reviewed journal article
Experimental identification of flow properties of a S355 structural steel for hot deformation processes
Schmicker, David; Paczulla, Stefan; Nitzschke, Steffen; Groschopp, Sven; Naumenko, Konstantin; Jüttner, Sven; Strackeljan, Jens
In: The journal of strain analysis for engineering design - London : Sage Publ., Bd. 50 (2015), Heft 2, S. 75-83
2013
Book chapter
Ganzheitliche Simulation der Schallemission eines Range-Extenders - vom Gasdruckverlauf zum Schalldruckverlauf
Duvigneau, Fabian; Nitzschke, Steffen; Göbel, Stefan; Ringwelski, Stefan; Gabbert, Ulrich; Strackeljan, Jens
In: Effizienz, Präzision, Qualität - 11. Magdeburger Maschinenbau-Tage ; 25. und 26. September 2013 an der OVGU: 11. Magdeburger Maschinenbau-Tage ; 25. und 26. September 2013 an der OVGU - Magdeburg: Univ., 2013, 2013, Paper A3-2, insgesamt 8 S.Kongress: Magdeburger Maschinenbau-Tage 11 (Magdeburg : 2013.09.25-26)
Identifikation des Einfluss konstruktiver Lagerparameter eines in Schwimmbuchsen gelagerten Rotorsystems
Daniel, Christian; Nitzschke, Steffen; Woschke, Elmar; Strackeljan, Jens
In: Schwingungen in Rotierenden Maschinen. - Berlin : Techn. Univ.; 2013, Paper-ID: ABS-211, insgesamt 10 S.Kongress: SIRM-Tagung; 10 (Berlin) : 2013.02.25-27
Numerical simulation of the dynamic behaviour of turbochargers under consideration of full-floating-ring bearings and ball bearings
Daniel, Christian; Göbel, Stefan; Nitzschke, Steffen; Woschke, Elmar; Strackeljan, Jens
In: International Conference on Vibration Problems. - Lisboa : APMTAC, insges. 10 S., 2013Kongress: ICOVP; 11 (Lisbon) : 2013.09.09-12
Einfluss der masseerhaltenden Kavitation auf gleitgelagerte Rotoren unter instationärer Belastung
Nitzschke, Steffen; Woschke, Elmar; Daniel, Christian; Strackeljan, Jens
In: Schwingungen in Rotierenden Maschinen. - Berlin : Techn. Univ.; 2013, Paper-ID: ABS-210, insgesamt 11 S.Kongress: SIRM-Tagung; 10 (Berlin) : 2013.02.25-27
2011
Book chapter
Numerische Simulation des instationären Verhaltens der Schwimmbuchsenlagerung in Turboladern
Daniel, Christian; Nitzschke, Steffen; Woschke, Elmar; Strackeljan, Jens
In: Schwingungen in Rotierenden Maschinen - neunte internationale Tagung ; 21. - 23. Februar 2011 Darmstadt, Deutschland ; SIRM 2011 ; Tagungsbeiträte, Proceedings: neunte internationale Tagung ; 21. - 23. Februar 2011 Darmstadt, Deutschland ; SIRM 2011 ; Tagungsbeiträte, Proceedings/ Tagung Schwingungen in Rotierenden Maschinen - neunte internationale Tagung ; 21. - 23. Februar 2011 Darmstadt, Deutschland ; SIRM 2011 ; Tagungsbeiträte, Proceedings - Darmstadt: Techn. Univ., Fachgebiet Strukturdynamik, 2011, 2011, Paper-ID 07, insgesamt 11 S.Kongress: SIRM-Tagung 9 (Darmstadt : 2011.03.21-23)
Entwicklung von Berechnungsverfahren zur numerischen Simulation des instationären Betriebs von Turboladern
Daniel, Christian; Nitzschke, Steffen; Woschke, Elmar; Strackeljan, Jens
In: Forschung und Innovation - 10. Magdeburger Maschinenbau-Tage ; 27. - 29. September 2011: 10. Magdeburger Maschinenbau-Tage ; 27. - 29. September 2011 - Magdeburg: Univ., 2011; Kasper, Roland . - 2011, insges. 10 S.Kongress: Magdeburger Maschinenbau-Tage 10 (Magdeburg : 2011.09.27-29)
Numerical runup simulation of a turbocharger with full floating ring bearings
Woschke, Elmar; Daniel, Christian; Nitzschke, Steffen; Strackeljan, Jens
In: Vibration problems ICOVP 2011: supplement ; the 10th International Conference on Vibration Problems / tefan Sega ..., ed.: supplement ; the 10th International Conference on Vibration Problems - Liberec: Technical University of Liberec, 2011; Segǐa, Štefan . - 2011, S. 334-339Kongress: ICOVP 10 (Prague : 2011.09.05-08)
Original article in peer-reviewed national journal
Simulation von Schwimmbuchsenlagerungen in Abgasturboladern
Nitzschke, Steffen; Woschke, Elmar; Daniel, Christian; Strackeljan, Jens
In: Visnyk Nacionalnogo Techninogo Universytetu Ukraïny "Kyïvskyj Politechninyj Instytut"/ Nacional'nyj techničnyj universytet Ukrainy "Kyivs'kyj politechničnyj instytut" - Kyïv, 2011, Bd. 61.2011, 2, S. 7-12[Ukrainisch-deutsche Konferenz für Maschinenbau "Moderne Werkstoffe und Technologien im Maschinenbau 2011" ; 1 (Kyiv) : 2011.04.13-14]